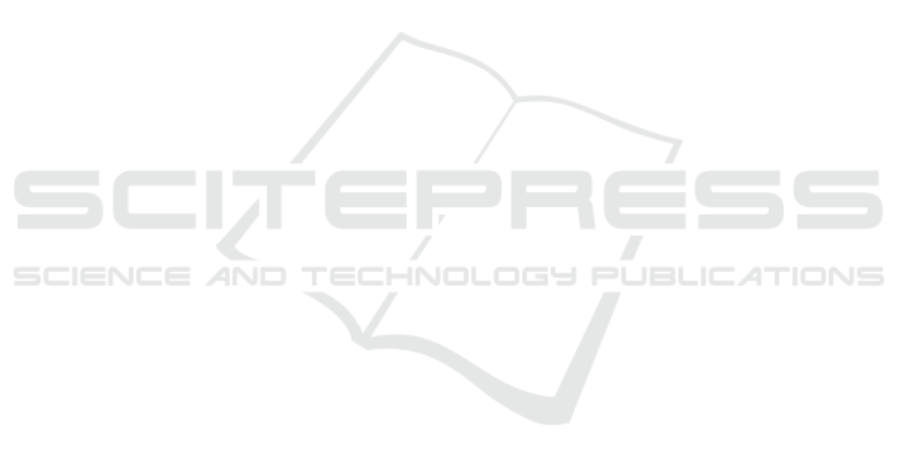
want to use a much more capable linear axis and more
suited and powerful servo motor to achieve similar
speeds and accelerations like the industrial robot. To
take further investigations regarding some quality is-
sues with our data from the distance sensor, we will
use a servo motor with a build in motor encoder for
tracking slippage or the loss of motor steps. The rea-
son further improvements for the test setup are nec-
essary is a unexpected jump in the sensor data of the
distance sensor clearly visible in figure 2 and figure 3.
We were also able to measure a drift in the distance
data during the movement of the robot and the exter-
nal axis. While a lost in distance between the external
axis and the robot during acceleration and decelera-
tion was expected, it should not occur during a con-
stant motion. Possible reasons for this could be a loss
of motor steps or the alignment of the linear axis to
the robot coordinate system. Therefore, another quite
important improvement would be the use of two laser
trackers to get external measured position data of the
robot and external axis movement. This would give
us further insights of how good the synchronization
between robot and external axis really is.
Furthermore, it is important to improve the consis-
tency of our data transmission. While the data trans-
mission for RSI on the robot and PLC side is based
on real time the exchange happened through the win-
dows interface of the soft PLC which is not real time
capable. Therefore, we have to implement a real time
interface to ensure a clean data transmission.
Another surprising finding was the behavior of
the FSD technology package. As discussed in sec-
tion 5.3, FSD exhibited a much faster transmission
rate (1 ms) than RSI (4 ms). However, the transmitted
data was only updated every 12 ms, counteracting the
advantages of the fast transfer rate. Furthermore, FSD
demonstrated a significant delay time about 100 ms
between the start of the robot movement and the first
change of the internal position data. This topic needs
some further investigation to clarify if we are able to
find a working configuration for FSD or if it is really
not suitable for our use case.
REFERENCES
Arbo, M. H., Eriksen, I., Sanfilippo, F., and Gravdahl, J. T.
(2020). Comparison of KVP and RSI for control-
ling KUKA robots over ROS. IFAC-PapersOnLine,
53(2):9841–9846.
Bi, Z. M., Liu, Y., Baumgartner, B., Culver, E., Sorokin,
J., Peters, A., Cox, B., Hunnicutt, J., Yurek, J., and
O’Shaughnessey, S. (2015). Reusing industrial robots
to achieve sustainability in small and medium-sized
enterprises (smes). Industrial Robot: An International
Journal, 42(3):264–273.
Bilancia, P., Schmidt, J., Raffaeli, R., Peruzzini, M., and
Pellicciari, M. (2023). An overview of industrial
robots control and programming approaches. Applied
Sciences, 13(4):2582.
Kaiser, B., Wolf, M., and Verl, A. (2022). Modular control
architecture for reconfigurable fabrication systems for
prefabrication in construction. In ISR Europe 2022;
54th International Symposium on Robotics, pages 1–
7. VDE.
Kaufmann, P., Braun, G., Buchheim, A., and Malecha, M.
(2019). Automated draping of wide textiles on double
curved surfaces. In Proceedings of the 16th Interna-
tional Conference on Informatics in Control, Automa-
tion and Robotics - Volume 2: ICINCO, pages 50–58.
INSTICC, SciTePress.
Kochoski, F., Dukovski, V., Samak, S., Cvetkoska, D., and
Petkoska, B. (2022). Manufacturing thermoplastic
composites by laser automatic tape placement tool-
less technology with dual robot system. Interna-
tional Journal of Engineering Research & Technology
(IJERT), 11(4).
Kritsch, S. (2018). Konzeption, Entwicklung und Va-
lidierung von Methoden zur Synchronisation von
Roboterbewegung und externer Vorschubachse. Mas-
ter thesis, University of Applied Sciences Fulda.
Mindermann, P., Bodea, S., Menges, A., and Gresser, G. T.
(2021). Development of an impregnation end-effector
with fiber tension monitoring for robotic coreless fila-
ment winding. Processes, 9(5):806.
M
¨
ollensiep, D., Gorlas, T., Kulessa, P., and Kuhlenk
¨
otter,
B. (2021). Real-time stiffness compensation and force
control of cooperating robots in robot-based double
sided incremental sheet forming. Production Engi-
neering, 15:683–699.
Stogl, D., Zumkeller, D., Navarro, S. E., Heilig, A., and
Hein, B. (2017). Tracking, reconstruction and grasp-
ing of unknown rotationally symmetrical objects from
a conveyor belt. In 2017 22nd IEEE International
Conference on Emerging Technologies and Factory
Automation (ETFA), pages 1–8. IEEE.
Winkler, A. and Such
`
y, J. (2013). Robot force/torque con-
trol in assembly tasks. IFAC Proceedings Volumes,
46(9):796–801.
ICINCO 2023 - 20th International Conference on Informatics in Control, Automation and Robotics
718