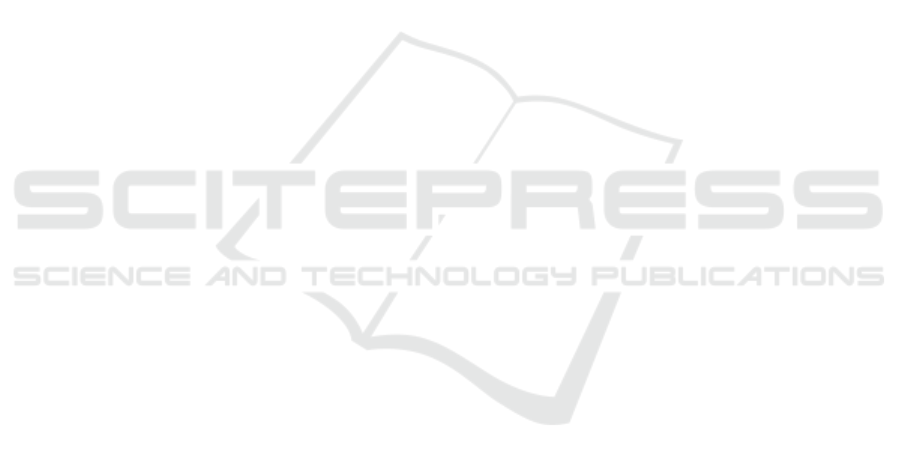
5 CONCLUSIONS & FUTURE
DEVELOPMENTS
In this paper, the authors propose an innovative con-
trol architecture for walk-through programming of an
industrial manipulator. The proposed solution aims at
allowing human operators to program industrial ma-
nipulators by directly teaching high-speed trajecto-
ries, while guaranteeing the operator’s safety. A ded-
icated safety controller has been developed to moni-
tor the kinematic configuration of the manipulator and
stop its motion whenever the risk of a collision with
the human operator becomes too high.
Given the results of the experimental validation,
the authors can state that the proposed architec-
ture successfully achieves a fruitful trade-off between
safety and productivity, by guaranteeing the opera-
tors’ safety and the possibility to directly record high-
velocity trajectories.
As far as future developments are concerned, the
authors foresee to integrate a tracking system to detect
and monitor in real-time the current position of each
link of the human operator, in order to obtain very
accurate occupancy volumes.
ACKNOWLEDGMENT
This work is partly supported by Regione Emilia-
Romagna under the agreement “Innovazione della
value proposition di Gaiotto Automation 2021-2025”
(grant number / CUP: E32C21001090009).
REFERENCES
(2015). Iso/ts 15066 - robots and robotic devices – collabo-
rative robots.
Ang, M. H., Lin, W., and Lim, S. (1999). A walk-through
programmed robot for welding in shipyards. Indus-
trial Robot: An International Journal, 26(5):377–388.
Ang, M. H., Wei, L., and Lim Ser Yong (2000). An in-
dustrial application of control of dynamic behavior of
robots-a walk-through programmed welding robot. In
IEEE International Conference on Robotics and Au-
tomation (ICRA), volume 3, pages 2352–2357 vol.3.
Ericson, C. (2005). Real-Time Collision Detection. Else-
vier.
Ferraguti, F., Bertuletti, M., Gambazza, M., and Ragaglia,
M. (2023). High-velocity walk-through programming
for industrial applications. Robotics and Computer-
Integrated Manufacturing, 81:102505.
Ferraguti, F., Talignani Landi, C., Costi, S., Bonf
`
e, M.,
Farsoni, S., Secchi, C., and Fantuzzi, C. (2020).
Safety barrier functions and multi-camera tracking for
human-robot shared environment. Robotics and Au-
tonomous Systems, 124:103388.
Ferretti, G., Magnani, G., and Rocco, P. (2009). Assigning
virtual tool dynamics to an industrial robot through an
admittance controller. In International Conference on
Advanced Robotics (ICAR), pages 1–6.
Gaiotto Automation Spa. Gaiotto website. https://www.
gaiotto.com/. Last checked on Sept 06, 2023.
ISO (2011a). Iso-2011-10218-1 - robots and robotic de-
vices - safety requirements for industrial robots - part
1: Robots.
ISO (2011b). Iso-2011-10218-2 - robots and robotic de-
vices - safety requirements for industrial robots - part
2: Robot systems and integration.
Jacinto-Villegas, J. M., Satler, M., Filippeschi, A., Berga-
masco, M., Ragaglia, M., Argiolas, A., Niccolini,
M., and Avizzano, C. A. (2017). A novel wearable
haptic controller for teleoperating robotic platforms.
IEEE Robotics and Automation Letters (IEEERAL),
2(4):2072–2079.
Michalos, G., Karagiannis, P., Dimitropulos, N., Andronas,
D., and Makris, S. (2021). Human Robot Collabora-
tion in Industrial Environments.
Pan, Z., Polden, J., Larkin, N., Van Duin, S., and Norrish, J.
(2012). Recent progress on programming methods for
industrial robots. Robotics and Computer-Integrated
Manufacturing, 28(2):87–94.
Ragaglia, M., Bascetta, L., Rocco, P., and Zanchettin, A. M.
(2014). Integration of perception, control and injury
knowledge for safe human-robot interaction. In IEEE
International Conference on Robotics and Automation
(ICRA), pages 1196–1202.
Ragaglia, M., Zanchettin, A. M., Bascetta, L., and Rocco,
P. (2016). Accurate sensorless lead-through program-
ming for lightweight robots in structured environ-
ments. Robotics and Computer-Integrated Manufac-
turing (RCIM), 39:9 – 21.
Ragaglia, M., Zanchettin, A. M., and Rocco, P. (2015).
Safety-aware trajectory scaling for human-robot col-
laboration with prediction of human occupancy.
In International Conference on Advanced Robotics
(ICAR), pages 85–90.
Ragaglia, M., Zanchettin, A. M., and Rocco, P. (2018).
Trajectory generation algorithm for safe human-robot
collaboration based on multiple depth sensor measure-
ments. Mechatronics (MECH), 55:267–281.
Tafazoli, S., Salcudean, S. E., Hashtrudi-Zaad, K., and
Lawrence, P. D. (2002). Impedance control of a tele-
operated excavator. IEEE Transactions on Control
Systems Technology (IEEECST), 10(3):355–367.
Tanzini, M., Jacinto-Villegas, J. M., Filippeschi, A., Nic-
colin, M., and Ragaglia, M. (2016). New interac-
tion metaphors to control a hydraulic working ma-
chine’s arm. In IEEE Symposium of Safety and rescue
Robotics (SSRR).
Tripicchio, P., Ruffaldi, E., Gasparello, P. S., Eguchi, S.,
Kusuno, J., Kitano, K., Yamada, M., Argiolas, A.,
Niccolini, M., Ragaglia, M., and Avizzano, C. A.
(2017). A stereo-panoramic telepresence system
for construction machines. Procedia Manufacturing
(PROCMAN), 11:1552 – 1559.
Villani, L. and De Schutter, J. (2008). Force Control, pages
161–185. Springer Berlin Heidelberg, Berlin, Heidel-
berg.
ICINCO 2023 - 20th International Conference on Informatics in Control, Automation and Robotics
510