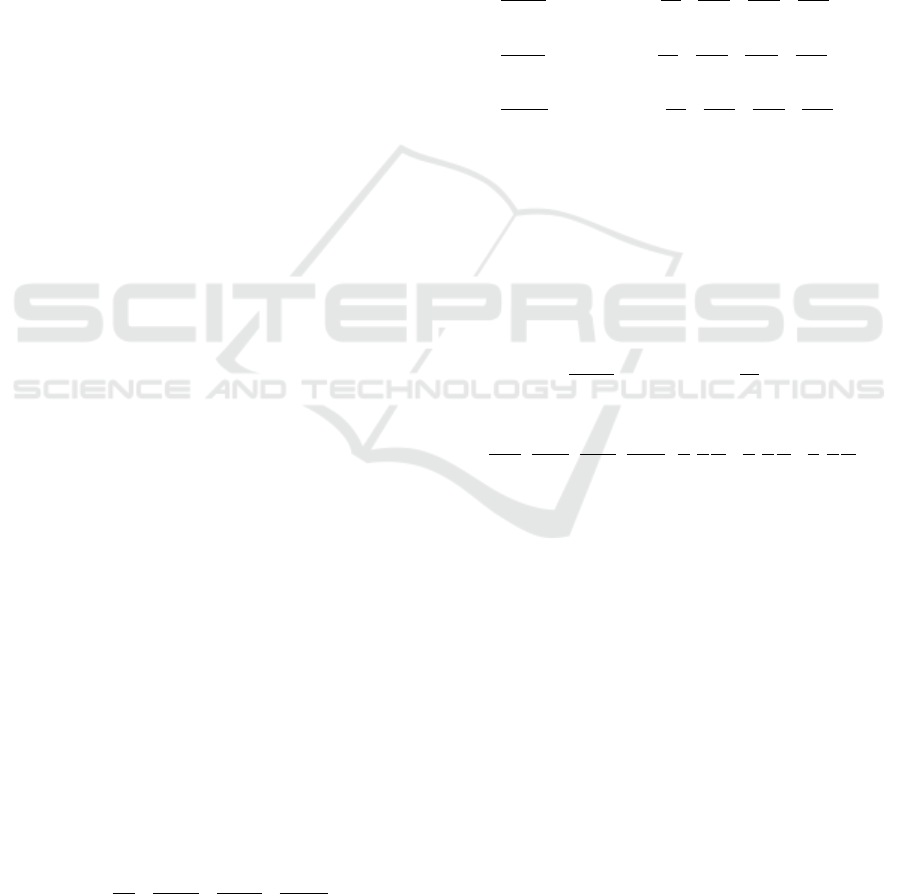
the implementation of the project, it is necessary to
use CFD simulation software to conduct simulation
tests, to see whether the optimization results meet the
expectations, and to see the impact of the chain
reaction of air flow changes on the thermal
environment of other channels.
2 CFD SOFTWARE
The research on the thermal environment of the
equipment room mainly evaluates the parameters of
the equipment room by establishing mathematical
models, establishing equal scale model tests and
using CFD simulation to simulate and construct the
thermal environment of the equipment room. The
conditions of the model experiment are strict, and the
research process is time-consuming and labor-
intensive. In contrast, CFD simulation modeling is
more efficient and convenient. CFD is an acronym for
Computational Fluid Dynamics. CFD simulation
software is based on the three conservation laws of
fluid flow (conservation of mass, conservation of
momentum and conservation of energy). It is used to
analyze, calculate and predict different physical
quantities (pressure, temperature, speed, etc.) in the
convection field through computer numerical
simulation and graphic images. It is mainly used to
solve various practical problems such as fluid flow,
heat conduction and momentum transfer in
engineering field. Different CFD software, its
functional focus and application areas are different,
can be subdivided into dozens of.
To construct the physical model of the machine
room and simulate the temperature and velocity fields
inside it, it is first necessary to determine the
mathematical model of the machine room, mainly the
control equation model, and the turbulence model.
Control equation modeling describes the basic
physical laws of fluids and macroscopic flow
phenomena. By solving these equations through
numerical methods, the distribution of physical
quantities such as velocity, pressure, and temperature
of the flow field in time and space can be obtained.
The control equation modeling starts with the
assumption that the machine room is well sealed, that
internal and external gases do not communicate
through doors and windows, and that the gas flow in
the machine room must satisfy the law of
conservation of mass, which is:
0
)()()(
z
w
y
v
x
u
t
Where u, v and w are the components of the
velocity vector u on the X, Y, and Z axes, respectively,
in m/s. ρ is the gas density in kg/m
3
, and t is the time
in s. This equation represents the mass conservation
of the fluid in the control volume. That is, the mass of
the inflow control body is equal to the mass of the
outflow control body.
The gas flow in the machine room also needs to
meet the law of conservation of momentum, so the
momentum components of the gas in the machine
room on the X, Y, and Z axes must meet the law of
conservation of momentum, which is:
F
zyxz
p
pwudiv
t
w
F
zyxy
p
pvudiv
t
v
F
zyxx
p
puudiv
t
u
z
zz
yz
xz
y
zyyyxy
x
zx
yx
xx
)(
)(
)(
)(
)(
)(
Where, p is the pressure on the fluid cell body, and
the unit is Pa;
F
n
is the force on the fluid element, the unit is N;
τ
nn
is the viscous stress on the fluid element, the
unit is N/m
2
.
Since the machine room contains heat exchange, it
must also meet the law of conservation of energy,
which is:
T
sgardT
cp
k
divuTdiv
t
T
)()(
)(
This formula can be expanded to:
T
ppp
ssss
s
z
T
c
k
zy
T
c
k
yx
T
c
k
xz
wc
y
vc
x
uc
t
c
)()()()(
where c
p
is the specific heat capacity, the unit is
J/kg•K;
T is the temperature, the unit is K;
k is the fluid heat transfer coefficient;
S
T
is the viscous dissipation term, which is the
fraction of mechanical energy converted to thermal
energy due to viscous action on the gas, the unit is J.
Turbulence modeling refers to the introduction of
additional equations to describe the turbulence effect
of the fluid on the basis of the control equation model,
and the turbulence characteristics of the flow field are
obtained by solving the control equation and the
additional equations through numerical methods.
Because of the slow flow rate of the gas in the
machine room, its pressure change is small, so the gas
density is mainly caused by the temperature change.
Therefore, it is assumed that the gas meets the
Boussinesq assumption, i.e., ignoring the change in
gas density caused by the change in pressure and only
CFD Simulation and Application of Semi-Closed Inclined Simple Cold Channel in a Data Center Server Room
543