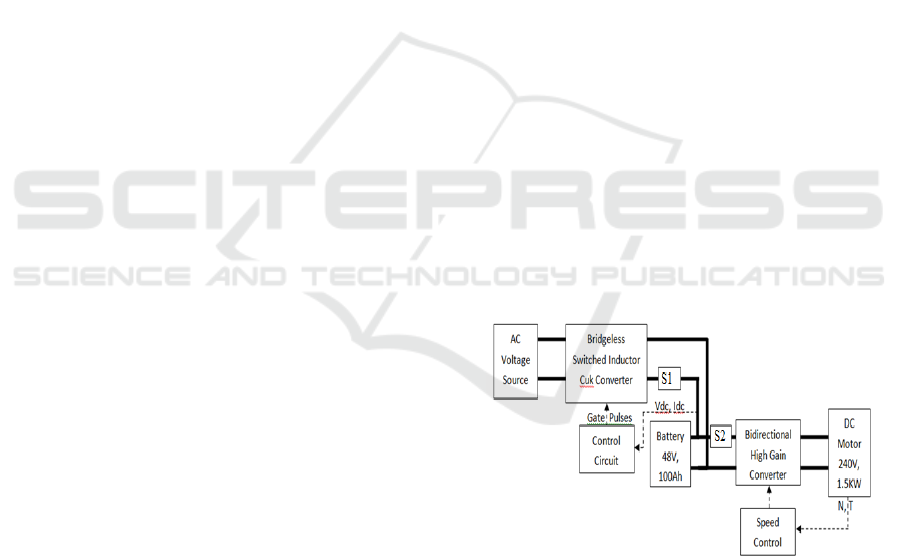
regulated (Rachid et al., 2022). To address these
issues with two-stage converters, numerous
researchers have proposed alternate single-stage
converter topologies for EVs/LEVs together with
enhanced power quality at the source side. The single-
stage converters provide a low component count, high
power density, and an easy-to-understand control
design (Habib,2018). A properly designed single-
stage converter configuration may also provide
superior efficiency compared to its two-stage
converter. The common buck converter's high supply
current distortion at the zero crossing and the standard
boost converter's constrained output voltage
capabilities exclude their possible usage as an APFC
in single-stage LEV converters. The disadvantages of
buck and boost derived converters are therefore
typically eliminated when utilizing buck-boost
derived converters. The Cuk model of buck-boost dc-
dc converters has the least amount of output and input
current ripple. Traditional buck-boost dc-dc
converters, on the other hand, are less suitable to
provide a transformerless single-stage conversion for
the LEVs due to their low gain capabilities. Due to
the low battery voltage, the transformerless charger
architecture in LEVs operates at an extremely low
duty ratio, which eventually affects the charger's
dynamic efficiency and performance. The common
buck converter's high supply current distortion at the
zero crossing and the standard boost converter's
constrained output voltage capabilities exclude their
possible usage as an APFC in single-stage LEV
converters. The disadvantages of buck and boost
derived converters are therefore typically eliminated
when utilizing buck-boost derived converters. The
Cuk model of buck-boost dc-dc converters has the
least amount of output and input current ripple.
Traditional buck-boost dc-dc converters, on the other
hand, are less suitable to provide a transformerless
single-stage conversion for the LEVs due to their low
gain capabilities. Due to the low battery voltage, the
transformerless charger architecture in LEVs
operates at an extremely low duty ratio, which
eventually affects the charger's dynamic efficiency
and performance. Therefore, the majority of single-
stage LEV converters based on conventional dc-dc
converters require a transformer in order to achieve
the required dc voltage gain. However, the
transformer drives up the cost and size of the charger.
The leakage inductance of the transformer also
increases the voltage stress between the parts. The
transformerless charger architecture for LEVs based
on improved power quality is still seldom ever
discussed in academia. coupling inductors, converter
cascading, the use of multipliers, interleaved front
end structures, switched inductors, and hybrid
switched inductor-capacitor structures are recent
developments (Khalid et,2021) (Das et al,2021).
However, in the case of linked inductors, the coupling
coefficient has a significant impact on the operational
parameters of the converter. The quadratic converter
is more effective than a cascaded converter at
adjusting for increasing voltage and current stresses.
As a remedy to these issues, a switching dual network
composed of two to three diodes, split type inductors,
or capacitors is proposed. This charger is costly, has
a challenging control system, and has larger magnetic
components due to the CCM operation. This research
presents a single-stage Cuk converter-based modified
power factor improved converter. Because the dcm
mode of operation eliminates the need for sensors, the
controller design is straightforward. The converter's
bridgeless design results in a significant reduction in
the number of components used. The proposed
converter is put to the test using constant voltage and
constant current control techniques with variable
input voltage conditions. Once the vehicle is running
on battery power, the motor is powered via a high
gain bidirectional converter. Regenerative braking
can be used and extend the vehicle's running time
because of the bidirectional property.
2 SYSTEM DESCRIPTION
The proposed system is provided below in Fig 1.
Fig 1: Proposed system Block diagram.
The ac supply is connected to the BSIC converter
in this case while the car is charging so that the battery
can be charged while switch 1 (S1) is ON and switch
2 (S2) is OFF. The battery serves as the load in this.
The control loop regulates the voltage and current of
the battery. S1 is OFF (the ac source is disconnected)
and S2 is ON (the motor is connected) when the car
starts. The battery serves as the supply in this. The
measured speed of the DC motor is fed into the speed
ISPES 2023 - International Conference on Intelligent and Sustainable Power and Energy Systems
108