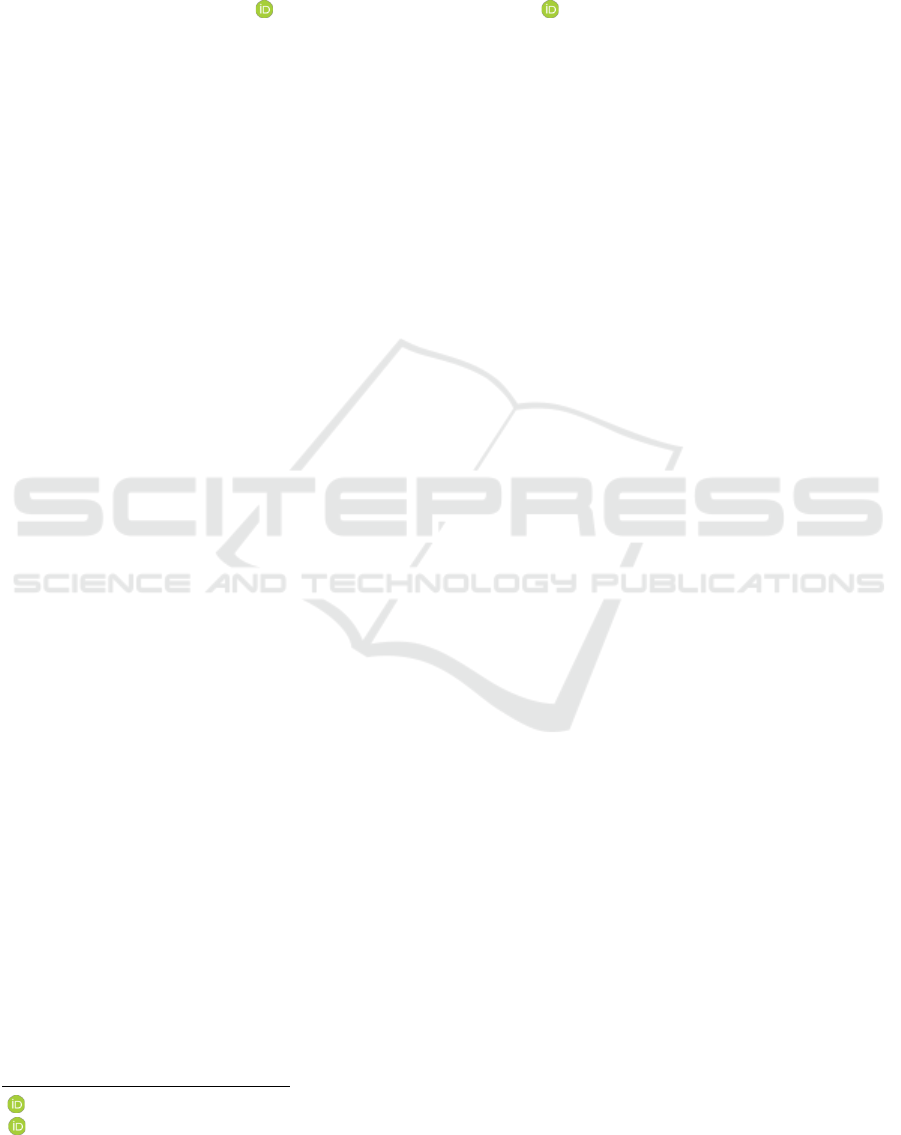
Testing Simulation in the River of Archimedes Screw Turbine on the
Cilember River in Bogor Using SolidWorks Software
Andi Saidah
a
, Audrey Deacy, Rajes Khana
b
and Jili Edo Pratama
Faculty of Engineering and Informatics, Universitas 17 Agustus 1945, Jakarta, Indonesia
Keywords: PLTMH, Archimedes Screw Turbine, Software SolidWorks, Simulation.
Abstract: In searching for a turbine suitable for microhydro power generation, it must align with the characteristics of
the river flow, such as the river head, water discharge, and flow velocity. In this study, the Archimedes screw
turbine was chosen because of its ease of manufacturing, high efficiency, and ability to handle appropriate
loads. Its operating principle involves the flow of water from the bottom of the screw turbine, entering the
space between the screw blades (buckets), and then exiting from the top of the turbine. The rotation of this
turbine rotor powers the electric generator connected to the top of the screw turbine, producing electrical
energy. Therefore, the design of the screw turbine and static load simulation using SolidWorks 2022 software
are necessary. The research aims to determine the extent of strain and stress distribution on the screw blades
when subjected to static loads. The design is based on calculations from literature and utilizes data collected
from the Cilember River in Bogor using the float method. From this data, a flow rate of 0.460 L/s and a water
head of 0.36 m are obtained. The calculated results also indicate a blade diameter of approximately 0.1866 m,
a turbine shaft diameter of 0.1 m, a turbine length of 0.8086 m, a turbine pitch of 0.1863 m, with a total of 4
threads on the turbine. The estimated potential power generation is around 8624 kW. Through static load
simulation, it is found that the maximum stress value reaches 3.59 x 10
6
N/𝑚
2
, and the maximum strain is
about 7.88 x 10
−3
mm at the examined node point, involving a total of 38871 elements.
1
INTRODUCTION
1.1 Electric Power Sources
In general, electric energy is defined as the primary
energy required for an electrical device to drive other
devices to function properly. Available energy is
divided into two types: renewable energy and non-
renewable energy. Renewable energy can be defined
as potential energy sources derived from nature and
can be continuously utilized for the sustainability of
the future. Use and process extra energy to create new
energy. Currently, renewable energy sources are still
being developed and will continue to be developed to
achieve efficiency.
On the other hand, non-renewable energy is
energy that will be depleted once used, with sources
that cannot be renewed, such as fossil fuels.
Various research studies have been conducted to find
electrical energy sources other than fossil fuels as
a
https://orcid.org/0009-0002-3065-2862
b
https://orcid.org/0000-0001-6062-6492
renewable energy sources. Some renewable turbine
power plants in Indonesia are Microhydro Power
Plants (PLTMH). This power plant creates small-
scale turbine generators that utilize the energy of flow
as a source of motion, such as river flow or
waterfalls, using the height of the waterfall, the
amount of water discharged, and water pressure. A
hydro turbine power generator is a device that
converts the flow energy into kinetic energy, and this
mechanical energy is then converted into electrical
energy using a generator. The type of turbine suitable
for PLTMH depends on the flow characteristics,
including head, available flow, and river speed. The
generator works by utilizing the waterfall height and
flow rate in the river and waterfall. The flow rate
drives the runner, causing mechanical energy that
makes the turbine and generator rotate. One type of
power generator that utilizes water flow is the
Archimedes screw turbine, which converts
mechanical energy from water into rotational
motion in the turbine.
Saidah, A., Deacy, A., Khana, R. and Pratama, J.
Testing Simulation in the River of Archimedes Screw Turbine on the Cilember River in Bogor Using SolidWorks Software.
DOI: 10.5220/0012583100003821
Paper published under CC license (CC BY-NC-ND 4.0)
In Proceedings of the 4th International Seminar and Call for Paper (ISCP UTA ’45 JAKARTA 2023), pages 399-405
ISBN: 978-989-758-691-0; ISSN: 2828-853X
Proceedings Copyright © 2024 by SCITEPRESS – Science and Technology Publications, Lda.
399