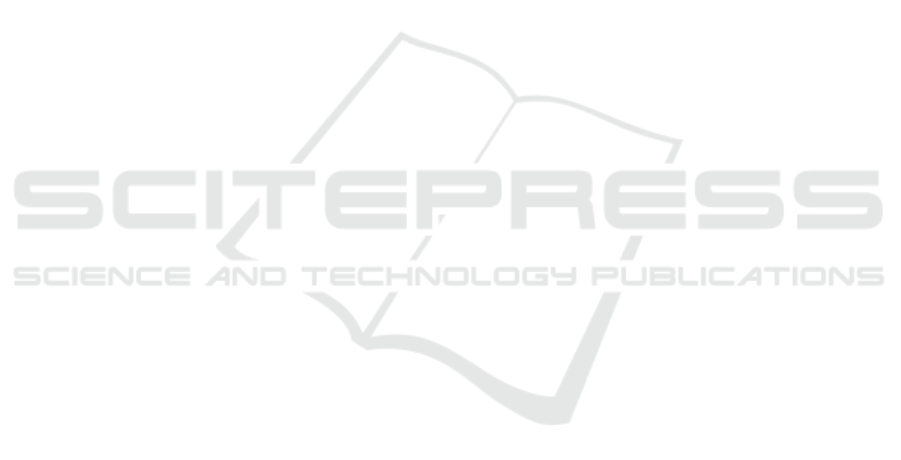
so electrolytic corrosion (an electrochemical reaction
that oxidizes metals) does not occur.
From the calculation of the corrosion rate of
plates using protection, better results are obtained
compared to no protection. This happens because of
the potential difference, then the electron current will
flow from the installed anode and will resist the
electron current from the nearby metal, so that the
metal turns into a cathode region. This is what slows
down the plate experiencing the corrosion rate while
on the contrary the plate without protection will
release electrons causing damage to the plate so that
it is easy to corrode.
4 CONCLUSION
1. From the results of the three experiments,
results were obtained that showed that
corrosion occurred which was characterized by
a decrease in the weight of objects.
2. After calculating the corrosion rate value using
the weight loss, the result is a slower corrosion
rate when using zinc anode protection and DC
current, followed by zinc anode protection and
finally without using protection.
3. From the three experiments, it was obtained that
the value of corrosion rate with protection with
zinc anode and DC current was 0.17 mpy or
corrosion rate was 17%, then with zinc anode
protection with a value of 0.22 mpy or corrosion
rate was 22% and the last one was without
protection the value obtained was 0.66 mpy or
corrosion rate was 66%.
4. With this research, it has become the initial stage
to be applied directly, so that the use of this
method can save routine repair costs in the
shipping industry.
REFERENCES
Yang, F., Yuan, M. M., Qiao, W. J., Li, N. N., & Du, B.
(2022). Mechanical degradation of Q345 weathering
steel and Q345 carbon steel under acid corrosion.
Advances in Materials Science and Engineering, 2022.
Di Sarno, L., Majidian, A., & Karagiannakis, G. (2021).
The effect of atmospheric corrosion on steel structures:
A state-of-the-art and case-study. Buildings, 11(12), 571.
Ma, Y., Li, Y., & Wang, F. (2009). Corrosion of low carbon
steel in atmospheric environments of different chloride
content. Corrosion science, 51(5), 997-1006.
Fan, Y., Liu, W., Li, S., Chowwanonthapunya, T.,
Wongpat, B., Zhao, Y., ... & Li, X. (2020). Evolution of
rust layers on carbon steel and weathering steel in high
humidity and heat marine atmospheric corrosion.
Journal of Materials Science & Technology, 39, 190-199.
Wu, H., Lei, H., Chen, Y. F., & Qiao, J. (2019). Comparison
on corrosion behaviour and mechanical properties of
structural steel exposed between urban industrial
atmosphere and laboratory simulated environment.
Construction and Building Materials, 211, 228-243.
Irshad, H. M., Toor, I. U., Badr, H. M., & Samad, M. A.
(2022). Evaluating the Flow Accelerated Corrosion and
Erosion–Corrosion Behavior of a Pipeline Grade
Carbon Steel (AISI 1030) for Sustainable Operations.
Sustainability, 14(8), 4819.
Alcántara, J., de la Fuente, D., Chico, B., Simancas, J., Díaz,
I., & Morcillo, M. (2017). Marine atmospheric corrosion
of carbon steel: A review. Materials, 10(4), 406.
Zhang, X., Zhou, X., & Nilsson, J. O. (2019). Corrosion
behaviour of AA6082 Al-Mg-Si alloy extrusion: The
influence of quench cooling rate. Corrosion Science,
150, 100-109
Zhang, Z., Zhang, F., Du, G., Li, G., Fan, W., Wang, Y., ...
& Wang, X. (2023). Effect of intermittent and
continuous direct current electric fields on the initial
corrosion of steel in simulated marine environment.
Materials Today Communications, 35, 105629.
Zhang, B., Wei, X. X., Wu, B., Wang, J., Shao, X. H., Yang,
L. X., ... & Ma, X. L. (2019). Chloride attack on the
passive film of duplex alloy. Corrosion Science, 154,
123-128.
Ohtsuka, T., & Tanaka, S. (2015). Monitoring the
development of rust layers on weathering steel using in
situ Raman spectroscopy under wet-and-dry cyclic
conditions. Journal of Solid State Electrochemistry, 19,
3559-3566.
Kamimura, T., Hara, S., Miyuki, H., Yamashita, M., &
Uchida, H. (2006). Composition and protective ability
of rust layer formed on weathering steel exposed to
various environments. Corrosion Science, 48(9), 2799-
2812.
Cheng, X., Jin, Z., Liu, M., & Li, X. (2017). Optimizing the
nickel content in weathering steels to enhance their
corrosion resistance in acidic atmospheres. Corrosion
Science, 115, 135-142.
Jeffrey, R., & Melchers, R. E. (2009). Corrosion of vertical
mild steel strips in seawater. Corrosion Science, 51(10),
2291-2297.
Feng, X., Yan, Q., Lu, X., Wu, T., Zhang, Y., Zuo, Y., &
Wang, J. (2020). Protection performance of the
submerged sacrificial anode on the steel reinforcement
in the conductive carbon fiber mortar column in splash
zones of marine environments. Corrosion Science, 174,
108818.
Bhandari, J., Khan, F., Abbassi, R., Garaniya, V., & Ojeda,
R. (2015). Modelling of pitting corrosion in marine and
offshore steel structures–A technical review. Journal of
Loss Prevention in the Process Industries, 37, 39-62.
Xu, Y., Huang, Y., Cai, F., Lu, D., & Wang, X. (2022).
Study on corrosion behavior and mechanism of AISI
4135 steel in marine environments based on field
exposure experiment. Science of The Total
Environment, 830, 154864.
Corrosion Rate of A36 Plate with Zinc Anode and Combination of Zinc Anode with Continuous Direct Current
435