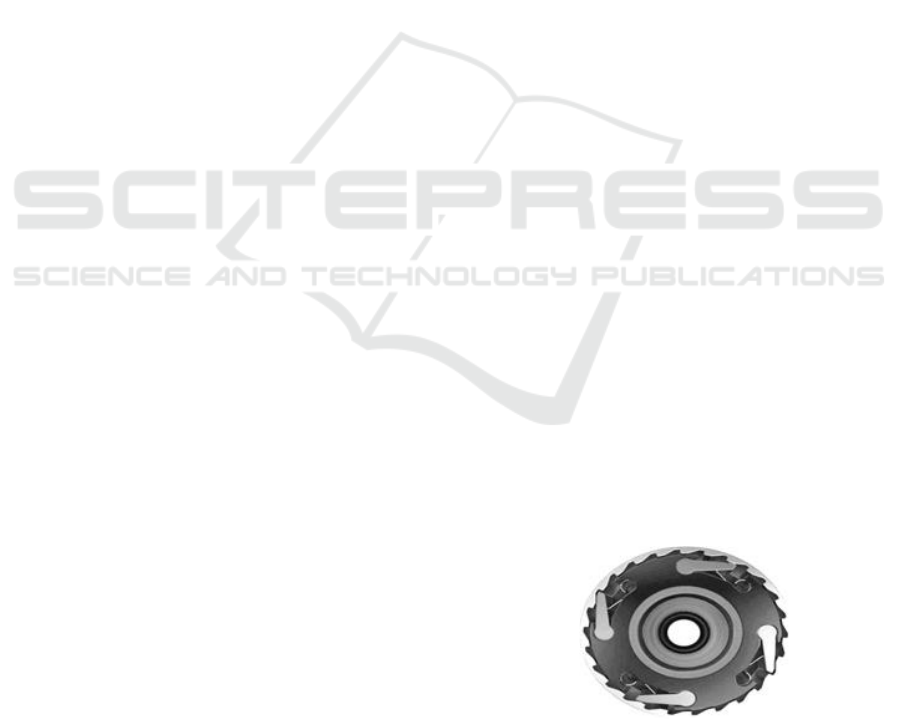
Anaconda Bulge Wave System
The movement of sea waves is used to fill flexible
tubes measuring 6-15 meters with a length of 150
meters. As the wave rises, water enters through the
valve, the fan with the change of wave, the tube
continues to fill and the pressure increases at the back
due to the swelling effect. A rear hydraulic system,
connected to an electric motor, operates this process
according to the height and speed of the wave and the
dimensions of the tube. Similar to the peristaltic
movement of human digestion.
Oyster Hydraulic Piston System
The hydraulic system is connected to the piston,
converting ocean wave energy into piston movement.
This movement is used to lift water into the high
pressure channel. Water is channeled through the
channel to a hydroelectric generator, producing
electrical energy. One of the main technologies today
is a device called "oyster" by the company
Aquamarine Power Ltd. Worldwide, the potential use
of hydraulic pistons is estimated to reach around 60
gigawatts (GW).
Pelamis System Attenuator
Oyster Hydraulic Piston System. The hydraulic
system is connected to the piston, converting ocean
wave energy into piston movement. This movement
is used to lift air into the high pressure channel. Air is
fed through these channels to a hydroelectric
generator, producing electrical energy. One of the
main technologies today is a device called "oyster" by
the company Aquamarine Power Ltd. Worldwide, the
potential use of hydraulic pistons is estimated at
around 60 gigawatts (GW).
Pelamis Attenuator System
Attenuators are formed by wave elements floating in
parallel, generating energy through the movement of
their interactions. This moves hydraulic components in
the tube, driving an electric generator like on the
Pelamis. The pelamis moves vertically and laterally,
consists of at least three segments, 500 meters long,
tube diameter 3 meters. Studies show that Pelamis is
180 meters long, 4 meters in diameter, at a depth of 50
meters, producing 750 Kw of electrical energy. The
movement of the waves flexes the Pelamis Structure,
utilized through a hydraulic take-off system that can
lengthen/contract, producing electricity that is
channeled through underground cables.
Oscillating Water Column
A Wave Power Plant (PLTO) with a Wave-Wind
(OWC) design produces energy from fluctuations in
air pressure in a container due to wave movement.
These fluctuations drive the wind turbine through
compressed air after passing through the control
valve. This turbine is connected to a generator and
converts movement into electrical energy.
Archimedes Wave Swing System
AWS uses Archimedes' concept to divide objects in
water into 3 categories: floating, floating, and
sinking. The movement of wave height variations is
converted into vertical movement. Inside the tube,
there is a stator and rotor. The stator is attached to the
seabed, while the rotor connected to the tube moves
up and down with the rhythm of the waves. Although
it is being tested in Europe and the United States,
AWS production costs tend to be higher than other
PLTO systems, limiting its widespread use.
Wave Dragon
Wave Dragon operates by collecting sea waves in
open water and channeling them into a pool. In the
pool, there is a water turbine with a low fall height.
The flow of water from the pool drives a water
turbine, converting the movement of water into
energy. In 2009, the first trial of Wave Dragon was
carried out in Nissum Bredning, Denmark,
successfully installing Wave Dragon with a capacity
of 7 MW (A. Hasnan, et al., 2010).
1.1 Freewheel
It is a sprocket that has a locked direction of rotation,
meaning that in a certain direction the shaft and the
driver move simultaneously, but if the direction of the
drive is opposite, the shaft continues to rotate in the
original direction so that it rotates freely.
Figure 1: Freewheel.
The main advantage of freewheels is that they are
more economical than freehubs (W. Dian, 2011).
ISCP UTA ’45 JAKARTA 2023 - THE INTERNATIONAL SEMINAR AND CALL FOR PAPER (ISCP) UTA ’45 JAKARTA
446