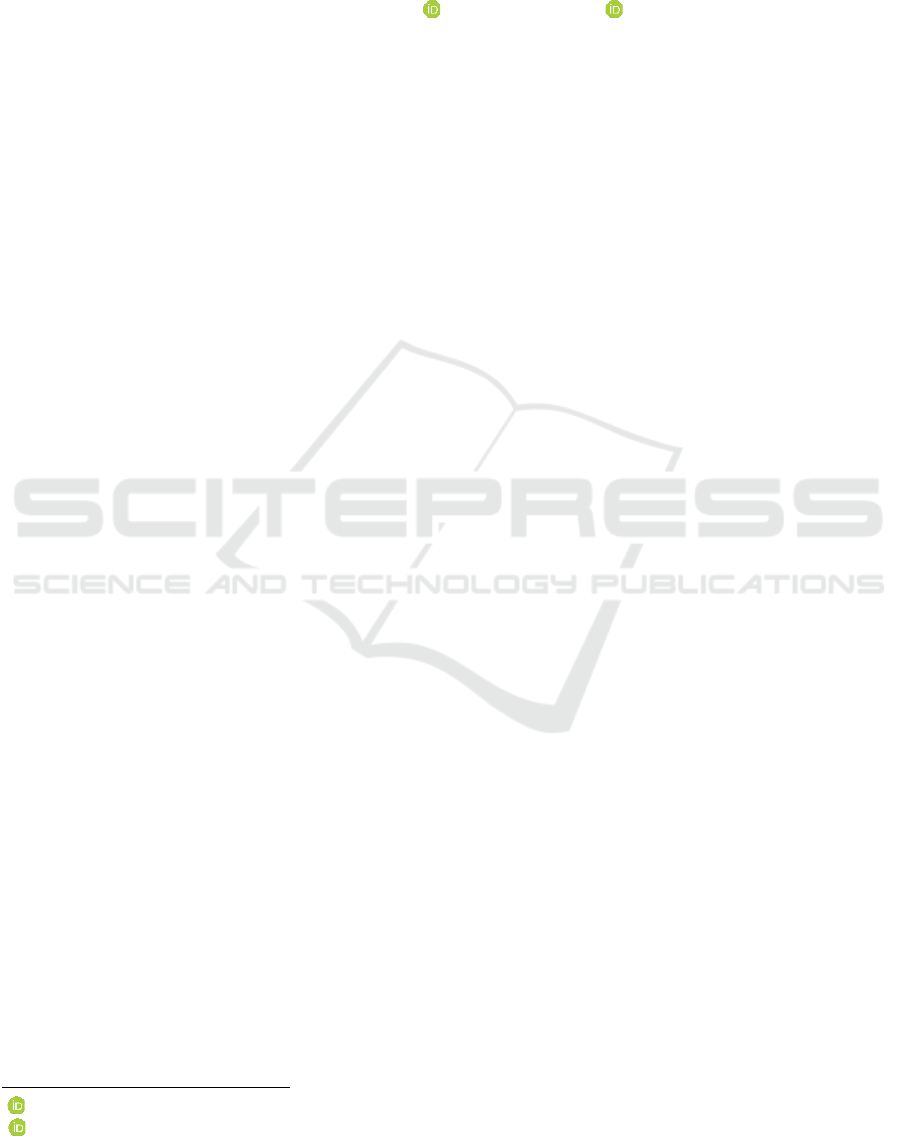
Analysis of Reduced Performance of 7.5 kW Hydraulic Pump Motor
on Telescopic Spreader Quayside Container Crane (QCC)
Erman Suherman
a
and Ahmad Rofii
b
Department of Electrical Engineering, Universitas 17 Agustus 1945 Jakarta, Jl. Sunter Permai Raya, Sunter Agung,
Tanjung Priok, Jakarta Utara, Indonesia
Keywords: Hydraulic Motor, Telescopic Spreader, Varnishing.
Abstract: Quayside Container Crane (QCC) is one of the heavy equipment used by the Nusantara Port Handal company.
The Telescopic Spreader is one of the equipment found on the Quayside Container Crane (QCC). The
mechanical power for the QCC work process comes from an induction motor or asynchronous motor. In
operation, lifting power often weakens, causing business processes to idle. QCC mechanical resources come
from induction motors or asynchronous motors, of course the work process depends on the reliability of the
motor. Based on monitoring and recording, the induction motor used by QCC with a capacity of 7.5 kW often
experiences a weakening of rotational power during busy work activities. After measuring the temperature
when the induction motor was loaded, the temperature reached 44
0
C and after measuring the motor stator
resistance value, it was 1200MΩ. Based on the analysis, the increase in motor temperature caused a decrease
in lifting power due to a decrease in the Insulator Resistance value which caused voltage leakage between the
armature windings. Motor resistance decreases due to the reduced ability of the stator insulator due to
increased heat, with a decrease in lifting capacity based on measurement results causing the vibration value
to increase from the threshold, thereby disrupting the construction of the stator armature. To overcome this,
re-varnishing of the insulator has been carried out which results in an increase in the resistance value of the
stator insulator.
1 INTRODUCTION
Indonesia is the largest archipelagic country in the
world. For this reason, Indonesia needs to manage
and develop a well-managed and developed port
industry (Setiono, 2010).
Handling of loading and unloading goods must be
in accordance with the provisions that have been set.
With these provisions, it is hoped that all stevedoring
companies can implement these provisions in order to
create a smooth flow of goods and harmony in work.
But in practice the handling of loading and unloading
is not always carried out smoothly and correctly, but
few of them ignore it. Most of these stevedoring
companies are only concerned with profits without
paying attention and thinking about the impacts that
will arise if the handling of loading and unloading is
carried out unsafely and incorrectly or not in
accordance with the provisions (Triatmodjo, 2006).
a
https://orcid.org/0009-0001-9164-1641
b
https://orcid.org/0009-0006-0677-9846
Quayside Container Crane (QCC) is one of the
heavy equipment used by Nusantara Pelabuhan
Handal. This tool stands and runs on rails on the edge
of the dock with a power source from a power plant
on land or with the power plant's own diesel engine.
The working principle is simple, the container from
the ship's hold is lifted up by a telescopic spreader
using a hoist system, then with horizontal movement
is carried using a trolley system towards the dock and
stops between the two crane legs (legs) to lower the
container until it is right above the truck chassis body.
The next movement is to return the empty telesopic
spreader from its position on the dock to the ship's
hold, and land the telescopic spreader on top of the
container to be unloaded next. (Lasse, 2012).
Container loading and unloading activities on
ships often occur system failures in the telescopic
spreader area. Especially often trips occur on spreader
pumps, telescopic positions from 20 feet to 40 feet
Suherman, E. and Rofii, A.
Analysis of Reduced Performance of 7.5 kW Hydraulic Pump Motor on Telescopic Spreader Quayside Container Crane (QCC).
DOI: 10.5220/0012584600003821
Paper published under CC license (CC BY-NC-ND 4.0)
In Proceedings of the 4th International Seminar and Call for Paper (ISCP UTA ’45 JAKARTA 2023), pages 449-457
ISBN: 978-989-758-691-0; ISSN: 2828-853X
Proceedings Copyright © 2024 by SCITEPRESS – Science and Technology Publications, Lda.
449