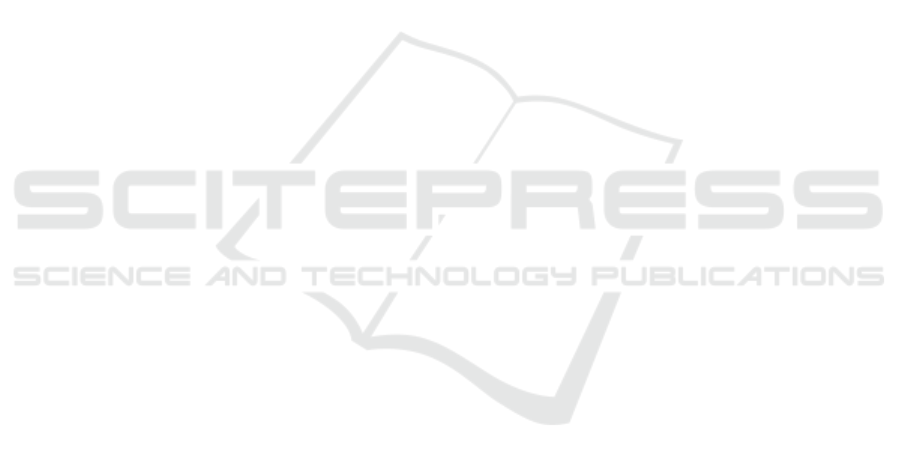
The ILP tool was built using the PULP Python
package (Foundation, 2023). The objective for the
tool was to create optimized schedules for single- or
multi-class fleets at a steady state of operations. The
constraints were developed to be modular in order to
be easily adapted to account for a range of different
availability requirements, including those that arise
from a fleet split across separate home ports, as was
demonstrated here. To evaluate the effectiveness of
the tool, fleet schedules were generated for asset fleets
with notional maintenance cycles. These will be com-
pared qualitatively to those produced using a genetic
algorithm-based fleet optimizer (Fee et al., 2019) that
is currently in use to support navy planning.
2 METHODOLOGY
To generate fleet schedules, an operations and mainte-
nance cycle, or OPCYCLE, is used as the main build-
ing block. These provide a semi-flexible mapping
of the asset’s readiness states over time. An asset’s
readiness state is the measure of its availability to per-
form operations. The schedule for a single asset is
made by repeating the OPCYCLE sequence over a
span of time. By choosing the offset between each as-
set schedule within a fleet, it is possible to distribute
available and unavailable states across the fleet sched-
ule to meet a set of requirements.
2.1 OPCYCLE and Readiness States
For the purposes of this report, the following readi-
ness states are used:
• Extended Readiness (ER): The asset is in deep
maintenance (usually in dry dock), so it is not con-
sidered employable and is not normally crewed.
• Restricted Readiness (RR): In this readiness state,
the asset is in shallow maintenance.
• Normal Readiness (NR): This is a period when the
asset can conduct limited domestic operations.
• High Readiness (HR): This is a period when the
asset is in the highest state of readiness and so it
can deploy on expeditionary operations and con-
duct the full spectrum of combat operations;
Each readiness state involves a different level of crew
training as well as availability of different equipment
on board. Remaining at the highest state of readiness
is taxing on both the crew and the asset and so can
only be maintained for a specific number of months.
Figure 1 shows an example of a typical OPCY-
CLE. Each block represents a time period where the
asset is at a particular readiness state and this se-
quence shows the transition from lowest readiness to
highest and back again.
Each asset starts in deep maintenance (ER) and
then begins its trajectory towards higher readiness
states. To start preparing the asset for operations, it
undergoes an intermediate RR stage. Once the asset
is out of the RR state, it will be at NR by default and
may be raised to HR at any time before the next ER
or RR period, whichever is first. Once the HR deploy-
ment is completed, the asset will either return to NR
or, if it is due for maintenance, enter the scheduled
ER or RR period.
2.1.1 OPCYCLE Repeats
If the schedule length is longer than the OPCYCLE,
the cycle is repeated. For example, for the OPCY-
CLE described in Figure 1, to generate a schedule of
30 time units long, the OPCYCLE would be repeated
twice. If the schedule length is not a multiple of the
length of the OPCYCLE, as shown in Figure 2 for
a fleet schedule of 20 time steps, partial OPCYCLE
repeats are used. Any time steps beyond t=19 are ig-
nored.
2.1.2 Sub-Operational Cycles
Since it is taxing on both the equipment and the crew
to maintain an asset at a higher state of readiness for
long periods of time, the operational cycles are often
broken up into smaller sub-segments, referred to here
as sub-OPCYLEs. Each sub-cycle contains a single
HR period and is delineated by short, shallow main-
tenance periods rather than the longer, deep mainte-
nance found at the start of the cycle.
Each sub-OPCYCLE includes a single sequence
of RR, NR, and HR readiness states, where the time
that the asset spends at NR and/or HR as well as the
placement of the HR state may vary. In Figure 3, the
two sub-OPCYCLEs are labelled.
2.1.3 Placement of the HR State
Following the RR stage in each sub-OPCYCLE, the
asset may enter the HR state or transition to NR. Once
at NR, the asset may be raised to HR at any time be-
fore the start of the next maintenance period (ER or
RR). In Figure 4, the first sub-OPCYCLE of the OP-
CYCLE from Figure 1 is examined. In Panel (a), the
HR state starts after the RR state ends, while in Panel
(b), (c) and (d), the start of the HR period is offset by
one, two and three time steps respectively.
For example, in Figure 1, the length of the HR
offset in the first sub-OPCYCLE is zero (directly af-
ter the RR period) and in the second sub-OPCYCLE
ICORES 2024 - 13th International Conference on Operations Research and Enterprise Systems
48