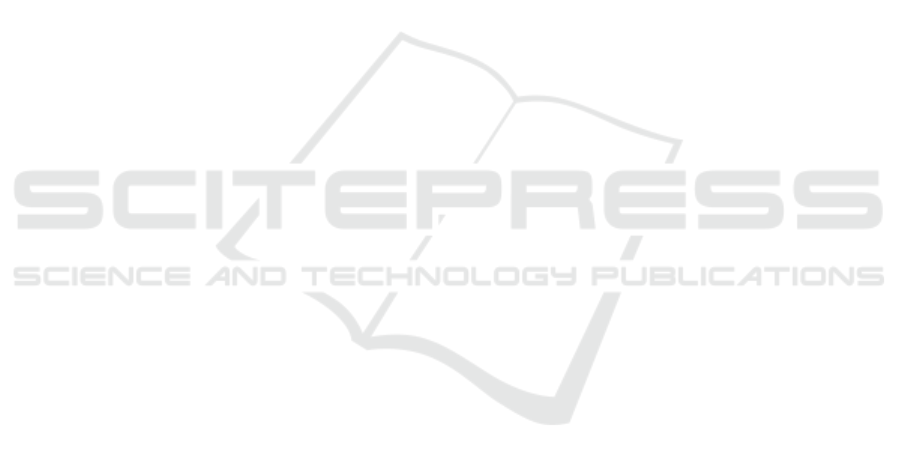
The work center includes a material loading ma-
chine for bar provision, capable of storing up to three
assortments of materials. Each material has its spe-
cific length and diameter and includes a certain quan-
tity of bars. Operators also can manually introduce
additional materials into the loading machine.
A conveyor belt serves as the conduit for trans-
ferring batches of uniform iron bars to an automatic
hydraulic cutter. This cutting system carries out se-
quential cuts according to cutting stock solutions pre-
calculated by the company’s optimizing software.
Following each cutting operation, the resulting
parts are released onto a transfer track. These are sub-
sequently moved to specific coordinates, a process fa-
cilitated by mechanical dividers.
The transfer track is positioned between two sym-
metrical and identical unloading stations. Here, the
parts are overturned among the stations and grouped
into homogeneous lots; i.e., lots that share the same
order code and have identical geometric attributes.
Two portals equipped with grippers are stationed at
the unloading stations. A portal empties its related
station by collecting all the available lots and allo-
cating the lots through lowering operations in a dedi-
cated stocking area. This area hosts identical parallel
buffers designed for lot collection. Importantly, ho-
mogeneous lots may be efficiently stacked together.
The portals offer flexibility by translating over the
stocking areas, while lots are transferred exclusively
lengthwise without altering their horizontal coordi-
nates. Furthermore, the grippers on each portal oper-
ate independently, allowing for the separate allocation
or retrieval of individual lots.
Once an order is consolidated, requests may ar-
rive from downstream departments. The portals are
then tasked with transporting the consolidated orders
to releasing depots, positioned on both sides of the
system. From these depots, the finalized orders leave
the work center for further processing or distribution.
In the work center, the automatic cutter plays a
critical role and acts as a bottleneck. It must halt
its operation if the produced parts cannot find an al-
location on the unloading stations, resulting in ma-
chine idle time. To maximize system efficiency, it
is needed to effectively utilize the unloading stations,
the buffers in stocking areas, and the portals. Given
the challenging nature of the problem at hand, we di-
vide the process into four distinct subproblems:
i) PATTERN SEQUENCING OPTIMIZATION: This
entails determining the optimal sequence of pat-
terns to minimize the spread of orders.
ii) PART PARTITIONING ON THE UNLOADING STA-
TIONS: Subsets of parts are allocated between the
two unloading stations to compose homogeneous
lots, limiting the number of offloading operations.
iii) OPTIMAL MANAGEMENT OF THE STOCKING
AREA: The lots on an unloading station are trans-
ferred through a portal on the buffers of the stock-
ing area, optimizing the occupied space and the
stacking of lots.
iv) SCHEDULE OF THE RELEASES OF CONSOLI-
DATED ORDERS: The timing and scheduling of
consolidated orders’ release are decided to mini-
mize the portal’s busy time.
Because of the limited space, in this paper we fo-
cus on addressing subproblem iii). We introduce a
sequential value correction heuristic (SVC) designed
to optimize the packing of lots onto parallel buffers
within a stocking area in a multi-objective fashion,
generating a pool of non-dominated solutions. Op-
timization criteria are the minimization of the occu-
pied space, the reduction of portal lowering opera-
tions, and the mitigation of order fragmentation. The
SVC embeds the concept of reachable points to effec-
tively describe the set of feasible destinations for lots
on the buffers.
2 PROBLEM DEFINITION
In this section, we formalize the problem by describ-
ing the problem features and details while introducing
some convenient notation.
The stocking area is modeled as a discretized grid
of locations (b, s) ∈ B × S, where the m buffers in B
correspond to rows and slots in S are the columns.
Each row has a width W given by the total width of
the |S| identical slots of size w.
We indicate with L the bill of orders and with I
the set of items (lots) to allocate, such that |I| = n.
Each order l is a subset of homogeneous items with
the same width w
i
= w
l
(assumed as multiple of w),
a release date r
i
, and a due date d
i
= d
l
. A subset of
items S
i
⊂ S can be trivially identified for each item i,
limited to eligible items s ∈ S such that s ≤ W − w
i
+
1. An order is considered fragmented if at least two
items i, j ∈ l are packed in different locations. We use
l
i
to refer to the order comprising item i.
Items arrive partitioned into unloading groups
(patterns) according to an ordered list P =<
p
1
, . . . , p
q
>. Each pattern is a subset of items fitting
within the capacity of the station W . Items must be
packed without overlapping on the buffer slots and a
safety slack (i.e., a minimum number of empty slots
between any two items) can be requested for applica-
tion extent. The only exception holds for items shar-
ICORES 2024 - 13th International Conference on Operations Research and Enterprise Systems
254