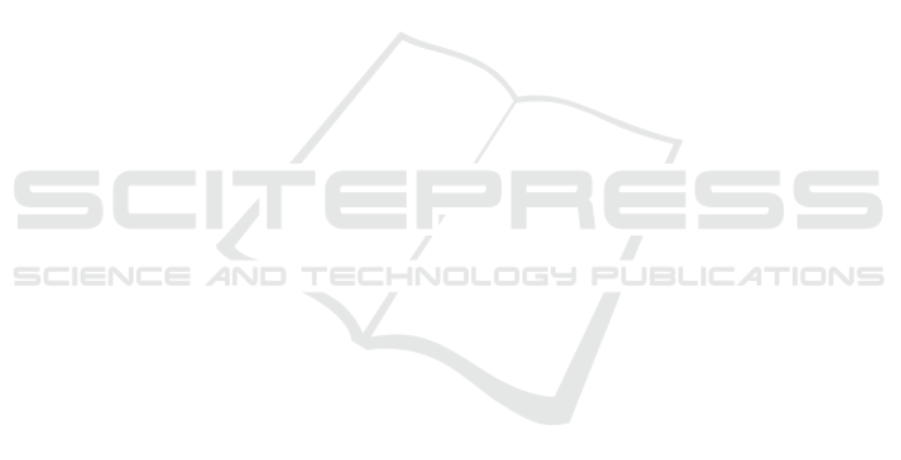
6 CONCLUSIONS
The work presented by Fei et al is widely consid-
ered to be the state-of-the-art for liquid-fabric inter-
action simulations. This paper has replaced APIC
with PolyPIC in their model and performed a com-
parison of the PolyPIC model with the APIC model
in the context of liquid-fabric interactions. Using
PolyPIC in place of APIC for liquid-fabric interac-
tion improves the dynamism of simulations, increas-
ing energy transfer between the fluid and cloth/yarn
and increasing the resolution of vorticial details and
small scale splashes. However, PolyPIC has a higher
computation cost over APIC and the reduced numer-
ical damping of PolyPIC also caused stability issues
requiring the use of a smaller time step. This require-
ment for smaller timesteps highlights the need for a
greater consideration of techniques to improve simu-
lation stability and inter-yarn collision detection. De-
spite this limitation, this paper demonstrates the po-
tential of PolyPIC as a method of improving liquid-
fabric interaction simulations based on PIC methods.
ACKNOWLEDGEMENTS
This research is supported by a Frank Greaves Simp-
son Scholarship from the University of Sheffield.
REFERENCES
Bergou, M., Wardetzky, M., Robinson, S., Audoly, B., and
Grinspun, E. (2008). Discrete elastic rods. ACM
Transactions on Graphics, 27(3):1–12.
Brackbill, J. and Ruppel, H. (1986). FLIP: A method for
adaptively zoned, particle-in-cell calculations of fluid
flows in two dimensions. Journal of Computational
Physics, 65:314–343.
Fang, Y., Li, M., Gao, M., and Jiang, C. (2019). Silly rub-
ber: an implicit material point method for simulating
non-equilibrated viscoelastic and elastoplastic solids.
ACM Transactions on Graphics, 38:1–13.
Fei, Y. R., Batty, C., Grinspun, E., and Zheng, C. (2018). A
multi-scale model for simulating liquid-fabric interac-
tions. ACM Trans. Graph., 37(4).
Fu, C., Guo, Q., Gast, T., Jiang, C., and Teran, J. (2017).
A polynomial particle-in-cell method. ACM Transac-
tions on Graphics, 36(6):222:1–222:12.
Grinspun, E., Hirani, A., Desbrun, M., and Schr
¨
oder, P.
(2003). Discrete Shells. In Proceedings of the 2003
ACM SIGGRAPH/Eurographics Symposium on Com-
puter Animation.
Harada, T., Koshizuka, S., and Kawaguchi, Y. (2007). Real-
time Fluid Simulation Coupled with Cloth. EG UK
Theory and Practice of Computer Graphics.
Harlow, F. H. (1962). The particle-in-cell method for nu-
merical solution of problems in fluid dynamics. Tech-
nical Report LADC-5288.
Huber, M., Pabst, S., and Straßer, W. (2011). Wet cloth
simulation. In International Conference on Computer
Graphics and Interactive Techniques.
Jiang, C., Schroeder, C., Selle, A., Teran, J., and Stomakhin,
A. (2015). The affine particle-in-cell method. ACM
Transactions on Graphics, 34(4):51:1–51:10.
Lenaerts, T., Adams, B., and Dutr
´
e, P. (2008). Porous
flow in particle-based fluid simulation. ACM Trans.
Graph., 27.
Li, M., Ferguson, Z., Schneider, T., Langlois, T., Zorin,
D., Panozzo, D., Jiang, C., and Kaufman, D. M.
(2020). Incremental potential contact: intersection-
and inversion-free, large-deformation dynamics. ACM
Transactions on Graphics, 39(4).
M
¨
uller, M., Heidelberger, B., Hennix, M., and Ratcliff,
J. (2007). Position based dynamics. Journal of
Visual Communication and Image Representation,
18(2):109–118.
Nielsen, M. B. and Østerby, O. (2013). A two-continua
approach to Eulerian simulation of water spray. ACM
Transactions on Graphics, 32(4):1–10.
Patkar, S. and Chaudhuri, P. (2013). Wetting of Porous
Solids. IEEE Transactions on Visualization and Com-
puter Graphics, 19(9):1592–1604.
Shao, X., Wu, W., and Wang, B. (2018). Position-based
simulation of cloth wetting phenomena. Computer
Animation and Virtual Worlds, 29(1):e1788.
SideFX (2023). Houdini - 3D modeling, animation, VFX,
look development, lighting and rendering | SideFX.
Stomakhin, A., Schroeder, C., Chai, L., Teran, J., and Selle,
A. (2013). A material point method for snow simula-
tion. ACM Transactions on Graphics, 32(4):1–10.
Stomakhin, A., Schroeder, C., Jiang, C., Chai, L., Teran,
J., and Selle, A. (2014). Augmented MPM for phase-
change and varied materials. ACM Transactions on
Graphics, 33(4):1–11.
Sulsky, D., Chen, Z., and Schreyer, H. L. (1994). A par-
ticle method for history-dependent materials. Com-
puter Methods in Applied Mechanics and Engineer-
ing, 118(1):179–196.
Zheng, Y., Chi, X., Chen, Y., and Wu, E. (2021). Stains on
imperfect textile. Virtual Reality & Intelligent Hard-
ware, 3:142–155.
Using the Polynomial Particle-in-Cell Method for Liquid-Fabric Interaction
251