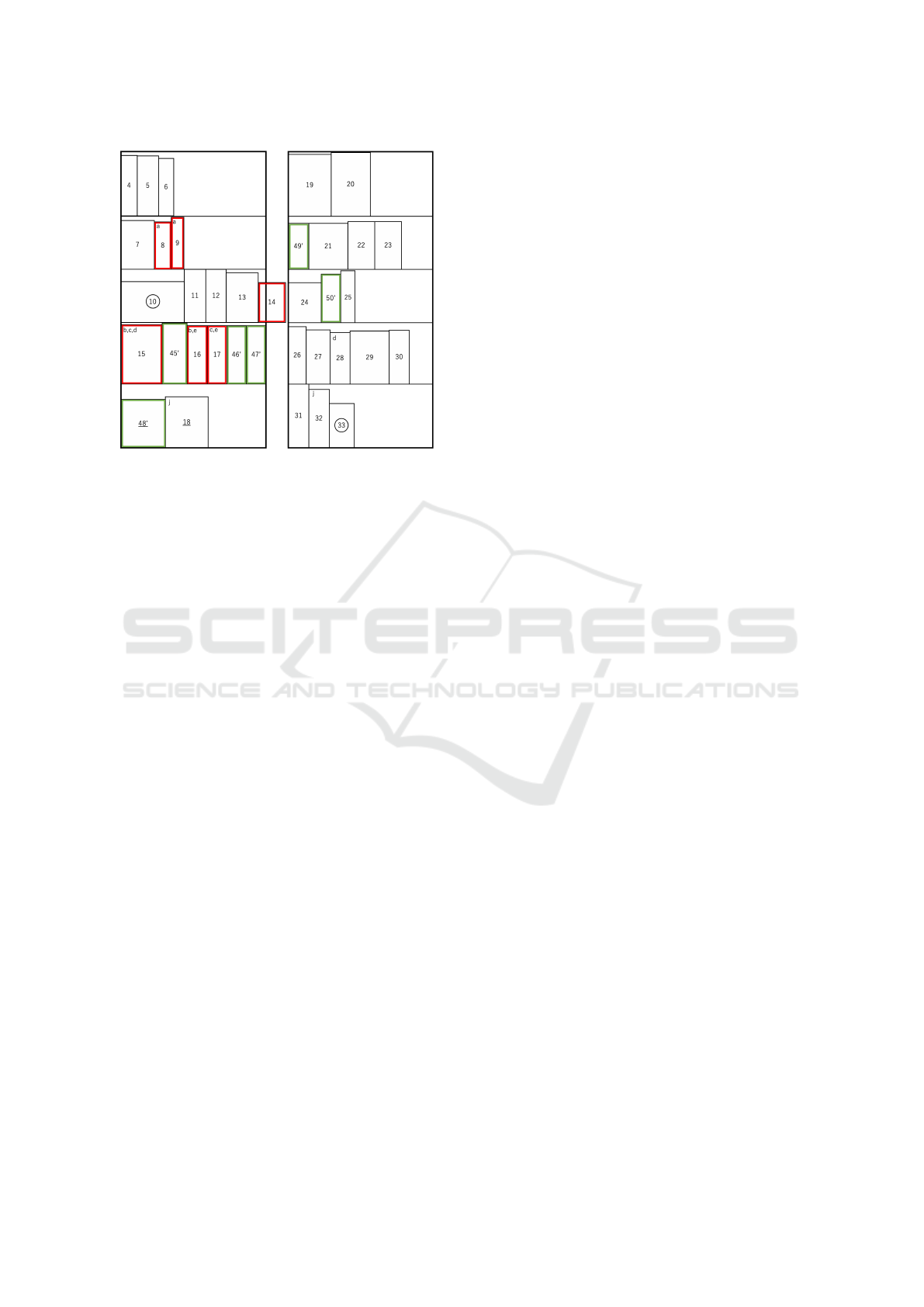
(a) shelf 0. (b) shelf 1.
Figure 9: Pre-optimize in-shelf product layouts for Shelf
’12B05Q’.
tion of AMRs. Based on the product assignments,
in-shelf product layout is generated by mathematical
optimization. The generated in-shelf product layout
is an effective layout, which allows for more efficient
and safer picking than the pre-optimized placement.
In the future, we will investigate methods that allow
interaction between the two optimization stages, such
as performing multiple product assignment optimiza-
tions only on shelves where the objective function
value is not improved, even though the two optimiza-
tion stages are independent. We will also discuss the
results of ongoing demonstration experiments using
real-world logistic data.
ACKNOWLEDGEMENTS
This work was supported in part by the Ministry of
Education, Culture, Sports, Science and Technology-
Japan, Grant–in–Aid for Scientific Research under
grant #JP19H01137 and #JP20H04018, and part
by the commissioned research by National Insti-
tute of Information and Communications Technology
(NICT), JAPAN. We are grateful to Yahata Neji Cor-
poration for providing us with real logistics operation
data.
REFERENCES
Gurobi optimizer homepage. https://www.gurobi.com/,
Last accessed 24 Jul 2023.
Anjos, M. F. and Vieira, M. V. (2021). Mathematical opti-
mization approach for facility layout on several rows.
Optimization Letters, 15(1):9–23.
Cravo, G. L. and Amaral, A. R. S. (2019). A grasp algo-
rithm for solving large-scale single row facility lay-
out problems. Computers & Operations Research,
106:49–61.
Dahlbeck, M., Fischer, A., and Hungerl
¨
ander, P. (2020). A
study of the relation between the single-row and the
double-row facility layout problem. Working paper.
Fogedby, H. C. (1994). L
´
evy flights in random environ-
ments. Physical review letters, 73(19):2517.
Hosseini-Nasab, H., Fereidouni, S., Ghomi, S. M. T. F., and
Fakhrzad, M. B. (2018). Classification of facility lay-
out problems: a review study. The International Jour-
nal of Advanced Manufacturing Technology, 94:957–
977.
Hungerl
¨
ander, P. and Rendl, F. (2013). A computational
study and survey of methods for the single-row facil-
ity layout problem. Computational Optimization and
Applications, 55:1–22.
Ihara, K. and Kato, S. (2020). Improving distribution-
based discrete particle swarm optimization using l
´
evy
flight. Australasian Joint Conference on Artificial In-
telligence, pages 189–200.
Ihara, K., Kato, S., Nakaya, T., Ogi, T., and Masuda, H.
(2019). Application of pso-based constrained combi-
nation optimization to segment assignment in shield
tunneling. Agents and Artificial Intelligence: 11th
International Conference, ICAART 2019, pages 166–
182.
Kennedy, J. and Eberhart, R. (1995). Particle swarm opti-
mization. 4:1942–1948.
Koster, R. D., Le-Duc, T., and Roodbergen, K. J. (2007).
Design and control of warehouse order picking: A lit-
erature review. 182(2):481–501.
Meskar, M., Eshghi, K., et al. (2020). An algorithm for
solving generalized single row facility layout prob-
lem. American Journal of Operations Research,
10(06):299.
P
´
erez-Gosende, P., Mula, J., and D
´
ıaz-Madro
˜
nero, M.
(2021). Facility layout planning. an extended litera-
ture review. International Journal of Production Re-
search, 59(12):3777–3816.
Tetsuyuki Takahama, S. S. (2005). Constrained optimiza-
tion by ε constrained particle swarm optimizer with
ε-level control. In Soft computing as transdisciplinary
science and technology, pages 1019–1029.
Watanabe, M., Ihara, K., Kato, S., and Sakuma, T. (2021).
Initialization effects for pso based storage assignment
optimization. pages pp. 494–495.
Wenming, W., Lubin, F., Ligang, L., and Peter, W. (2018).
Miqp-based layout design for building interiors. Com-
puter Graphics Forum, 37(2).
Xin-She Yang, S. D. (2010). Engineering optimisation by
cuckoo search. International Journal of Mathemati-
cal Modelling and Numerical Optimisation, 1(4):330–
343.
Generating Products Placement in Warehouse Using BLPSO and MIQCPs
461