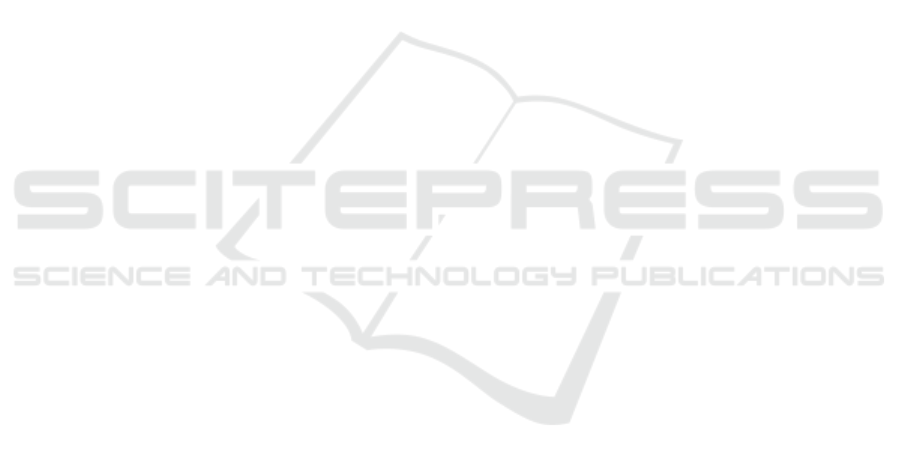
prediction is considered during the prototyping phase
and construction of the manufacturing machine, the
relevance of features can inform the selection of phys-
ical sensors to be deployed on the machine. The pro-
totype machine is equipped with a larger set of sen-
sors, and only after evaluating the prediction models
is the final set of relevant sensors determined.
Finally, besides the direct relation to the manu-
facturing case study, we see the benefit of deploying
smaller, less complex, and ideally interpretable mod-
els (Breiman, 2001; Rudin et al., 2022). At the same
time, there is a trade-off between simplicity and ac-
curacy, referred to as the Occam dilemma (Breiman,
2001). The simpler a model is made, the less accurate
it gets. We see this in the case study from the error
difference between the simpler decision tree vs. the
more complex gradient-boosting trees or random for-
est. By applying explainability methods to reduce the
feature space, we again reduce the model complexity,
making the final model more interpretable.
6 CONCLUSION
This study showcases the potential of combining ML
and explainability techniques to enhance the perfor-
mance of predictive models of surface quality in the
manufacturing sector, specifically in the context of
the milling process. Despite the limitations imposed
by data availability, our approach successfully lever-
ages less data-rich ML models, enhancing their effi-
cacy through feature selection based on explainability
methods.
For future work, we are interested in extending the
application of explainability methods in ML models
to other manufacturing processes of our partners be-
yond milling to create a more comprehensive predic-
tive system. Additionally, utilizing these ML models
as digital twins for the corresponding physical ma-
chinery opens new avenues for employing parameter
optimization methods. This integration not only en-
hances the accuracy of the models but also provides
an opportunity for real-time fine-tuning of machine
operations, thereby potentially improving efficiency
and reducing costs.
ACKNOWLEDGMENTS
This work is funded by the European Union under
grant agreement number 101091783 (MARS Project)
and as part of the Horizon Europe HORIZON-CL4-
2022-TWIN-TRANSITION-01-03.
REFERENCES
Bento, V., Kohler, M., Diaz, P., Mendoza, L., and Pacheco,
M. A. (2021). Improving deep learning performance
by using explainable artificial intelligence (xai) ap-
proaches. Discover Artificial Intelligence, 1:1–11.
Bins, J. and Draper, B. A. (2001). Feature selection from
huge feature sets. In Proceedings Eighth IEEE Inter-
national Conference on Computer Vision. ICCV 2001,
volume 2, pages 159–165. IEEE.
Breiman, L. (2001). Statistical Modeling: The Two Cul-
tures (with comments and a rejoinder by the author).
Statistical Science, 16(3):199–231.
Brusa, E., Cibrario, L., Delprete, C., and Di Maggio, L.
(2023). Explainable ai for machine fault diagno-
sis: Understanding features’ contribution in machine
learning models for industrial condition monitoring.
Applied Sciences, 13(4):20–38.
Chouhad, H., Mansori, M. E., Knoblauch, R., and Corleto,
C. (2021). Smart data driven defect detection method
for surface quality control in manufacturing. Meas.
Sci. Technol., 32(105403):16pp.
Fertig, A., Weigold, M., and Chen, Y. (2022). Machine
learning based quality prediction for milling processes
using internal machine tool data. Advances in Indus-
trial and Manufacturing Engineering, 4:100074.
Huang, N., Lu, G., and Xu, D. (2016). A permutation
importance-based feature selection method for short-
term electricity load forecasting using random forest.
Energies, 9(10):767.
Kummar, S. L. (2017). State of the art-intense review on
artificial intelligence systems application in process
planning and manufacturing. Engineering Applica-
tions of Artificial Intelligence, 65:294–329.
Kwon, H. J., Koo, H. I., and Cho, N. I. (2023). Un-
derstanding and explaining convolutional neural net-
works based on inverse approach. Cogn. Syst. Res.,
77:142–152.
Lampathaki, F., Agostinho, C., Glikman, Y., and Sesana, M.
(2021). Moving from ‘black box’ to ‘glass box’ arti-
ficial intelligence in manufacturing with xmanai. In
2021 IEEE International Conference on Engineering,
Technology and Innovation (ICE/ITMC). Cardiff, UK.
Lozano-Murcia, C., Romero, F. P., Serrano-Guerrero, J.,
and Olivas, J. A. (2023). A comparison between
explainable machine learning methods for classifica-
tion and regression problems in the actuarial context.
Mathematics, 11(14):3088.
Mokhtari Homami, R., Fadaei Tehrani, A., Mirzadeh, H.,
Movahedi, B., and Azimifar, F. (2014). Optimization
of turning process using artificial intelligence technol-
ogy. The International Journal of Advanced Manufac-
turing Technology, 70:1205–1217.
Mundada, V. and Narala, S. K. R. (2018). Optimization
of milling operations using artificial neural networks
(ann) and simulated annealing algorithm (saa). Mate-
rials Today: Proceedings, 5(2):4971–4985.
Myles, A. J., Feudale, R. N., Liu, Y., Woody, N. A., and
Brown, S. D. (2004). An introduction to decision tree
ICAART 2024 - 16th International Conference on Agents and Artificial Intelligence
904