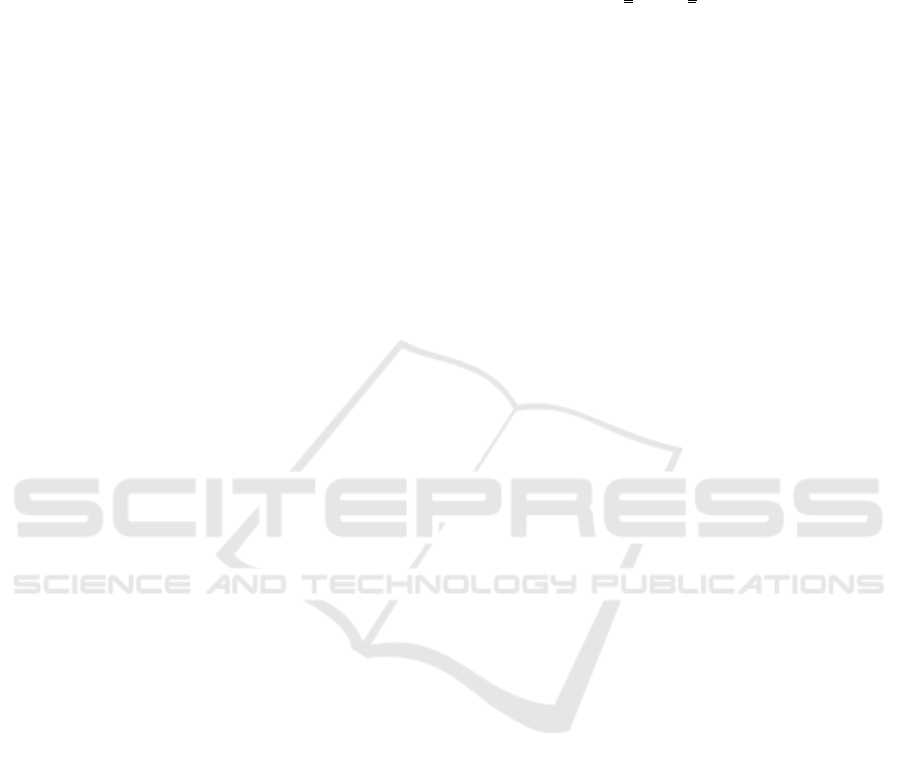
hicle, depending on several factors, such as ambient
temperature and algorithm settings. All energy sav-
ings of eco-comfort result in savings on operational
costs, with a possible reduction in thermal comfort.
Eco-driving also reduces the energy consumption of
the vehicle powertrain, depending on the maximum
acceleration set in the algorithm and the maximum
speed. However, such a reduction comes with an
additional traveling time, which increases the labor
costs. The settings of eco-driving needs to be care-
fully chosen depending on the electricity price and the
labor costs, to provide operational savings.
Lastly, results also show that using all the eco-
functions in the multi-layer EMS results in a reduc-
tion in energy consumption in the entire fleet. How-
ever, the operational cost savings related to energy
consumption are slightly reduced by the fact that eco-
charging charges the fleet preferably when the elec-
tricity prices are lower. Likewise, the traveling time of
each vehicle is increased by the effect of eco-driving
and decreased by the effect of eco-routing. The ben-
efits of these eco-functions can cancel each other if
eco-driving is not properly tuned, leading to higher
labour costs. Therefore, an additional simulation is
run to show a hypothetical case in which the benefits
of both eco-driving and eco-routing can be added to
each other, due to the costs of energy-related savings
being comparable to the labor-related savings.
ACKNOWLEDGEMENTS
This research has received funding from the European
Union’s Horizon 2020 research and innovation pro-
gramme under grant No 101006943, title of URBAN-
IZED.
REFERENCES
Ahmadi, P. (2019). Environmental impacts and behav-
ioral drivers of deep decarbonization for transporta-
tion through electric vehicles. Journal of Cleaner Pro-
duction, 225:1209–1219.
Ajanovi
´
c, Z. et al. (2018). A novel model-based heuris-
tic for energy-optimal motion planning for automated
driving. 15th IFAC Symposium CTS, 51(9):255–260.
Anosike, A. et al. (2023). Exploring the challenges of elec-
tric vehicle adoption in final mile parcel delivery. In-
ternational Journal of Logistics Research and Appli-
cations, 26(6):683–707.
Cataldo-D
´
ıaz, C. et al. (2024). Mathematical models for the
electric vehicle routing problem with time windows
considering different aspects of the charging process.
Operational Research, 24(1):1.
Donateo, T. et al. (2014). A method to estimate the environ-
mental impact of an electric city car during six months
of testing in an italian city. Journal of Power Sources,
270:487–498.
European Comission (2022). Hourly labour costs
ranged from C8 to C51 in the EU. https:
//ec.europa.eu/eurostat/web/products-eurostat-news/
w/DDN-20230330-3. Accessed:01-02-2024.
Ewert, A. et al. (2020). Small and light electric vehicles:
An analysis of feasible transport impacts and oppor-
tunities for improved urban land use. Sustainability,
12(19).
Gao, Z. et al. (2023). Electric vehicle lifecycle carbon
emission reduction: A review. Carbon Neutralization,
2(5):528–550.
Geerts, D. et al. (2022). Optimal charging of electric ve-
hicle fleets: Minimizing battery degradation and grid
congestion using battery storage systems. In Second
International Conference SMART, pages 1–11. IEEE.
Han, J., Vahidi, A., and Sciarretta, A. (2019). Fundamen-
tals of energy efficient driving for combustion engine
and electric vehicles: An optimal control perspective.
Automatica, 103:558–572.
Kallehauge, B. et al. (2005). Vehicle routing problem with
time windows. Springer.
Kwak, K. H. et al. (2023). Thermal comfort-conscious
eco-climate control for electric vehicles using model
predictive control. Control Engineering Practice,
136:105527.
Lacombe, R. (2023). Distributed optimization for the opti-
mal control of electric vehicle fleets.
Lera-Romero, G. et al. (2024). A branch-cut-and-price al-
gorithm for the time-dependent electric vehicle rout-
ing problem with time windows. European Journal of
Operational Research, 312(3):978–995.
Medina, R. et al. (2020). Multi-layer predictive energy man-
agement system for battery electric vehicles. IFAC-
PapersOnLine, 53(2):14167–14172.
Medina, R. et al. (2023). Urbanized D4.4: Optimised self-
adaptive, multi-layer EMS design and virtual valida-
tion fleet management algorithm. Technical report,
European Union Horizon 2020, research and innova-
tion programme.
Naeem, H. M. Y. (2023). Eco-driving Control of Electric
Vehicle with Realistic Constraints. PhD thesis, Capital
University.
Purnot, T. et al. (2021). Urbanized D2.1: Mission profiles,
KPIs, assessment plan, List of vehicle requirements,
design specifications and shared interfaces. Technical
report, European Union Horizon 2020, research and
innovation programme.
Rath, S. et al. (2023). Real-time optimal charging strat-
egy for a fleet of electric vehicles minimizing battery
degradation. In SEFET, pages 1–8. IEEE.
Sendek-Matysiak, E. et al. (2022). Total cost of ownership
of light commercial electrical vehicles in city logis-
tics. Energies, 15(22).
Siragusa, C. et al. (2022). Electric vehicles performing last-
mile delivery in B2C e-commerce: An economic and
Multi-Layer Energy Management System for Cost Optimization of Battery Electric Vehicle Fleets
123