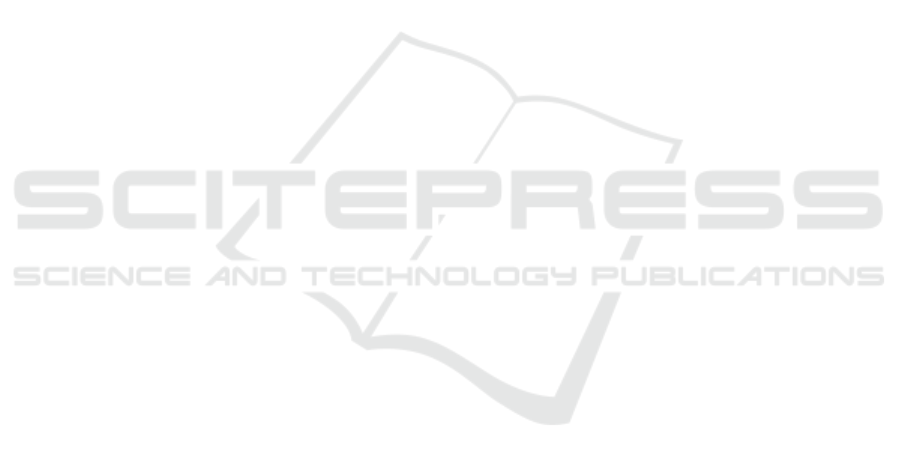
ACKNOWLEDGEMENTS
The author thanks the two anonymous reviewers for
their detailed comments which helped to improve the
readability of the paper.
The author is the head of the Design Theory
and Similarity Mechanics Group at the University of
Stuttgart, Germany, and supervises in this function the
PhD research works in the group. All the various re-
sults of the different packing, piping and routing al-
gorithms shown are parts of these PhD works in the
research group and are cited accordingly.
The funding of parts of this research by the Eu-
ropean Commission in the framework of the H2020
CS2 project PHAROS (see https://cordis.europa.eu/
project/id/865044 for details), the German ministry
for education and research in the context of the MA-
NUNET project FORTIFIER in the research pro-
gram “Future of Value Creation” (grant number
MNET20/ICT-3763) and of the ITEA3 project IDE-
ALISM (see https://itea4.org/project/idealism.html
for details) is greatly acknowledged.
The findings in this research do not necessarily re-
flect the opinion of the funding agencies.
REFERENCES
Arseniev-Koehler, A. (2022). Theoretical foundations and
limits of word embeddings: What types of meaning
can they capture? Department of Sociology, Univer-
sity of California, Los Angeles.
Cagan, J., Shimada, K., and Yin, S. (2002). A survey of
computational approaches to three-dimensional layout
problems. Computer-Aided Design, 34(8):597–611.
Eheim, M., Kaiser, D., and Weil, R. (2021). On automa-
tion along the automotive wire harness value chain.
In Weißgraeber, P., Heieck, F., and Ackermann, C.,
editors, Advances in Automotive Production Technol-
ogy – Theory and Application, pages 178–186, Berlin.
Springer.
Gomez-Perez, J. M., Denaux, R., and Garcia-Silva, A.
(2020). Understanding Word Embeddings and Lan-
guage Models, pages 17–31. Springer International
Publishing, Cham.
Hahn, N. and Rudolph, S. (2023). Digitale Durchg
¨
an-
gigkeit, Konsistenz und Interoperabilit
¨
at im Produkt-
lebenszyklus mit graphenbasierten Entwurfssprachen
(in German). In VDI Automation Congress, pages
443–458, Baden-Baden. VDI Verlag.
IILS mbH (2023). Design Cockpit 43
®
. https://www.iils.de.
Karlsson, T.,
˚
Ablad, E., Hermansson, T., Carlson, J., and
Tenf
¨
alt, G. (2023). Automatic cable harness layout
routing in a customizable 3D environment. Computer-
Aided Design, page 14.
Kirkpatrick, S., Gelatt, C. D., and Vecchi, M. P. (1983).
Optimization by simulated annealing. Science,
220(4598):671–680.
Leung, J. Y.-T., Tam, T. W., Wong, C., Young, G. H.,
and Chin, F. Y. (1990). Packing squares into a
square. Journal of Parallel and Distributed Comput-
ing, 10(3):271–275.
Neumaier, M., Kranemann, S., Kazmeier, B., and Rudolph,
S. (2022). Automated piping in an Airbus A320
landing gear bay using graph-based design languages.
Aerospace, 9(3).
Pahl, G. and Beitz, W. (1996). Engineering Design. A Sys-
tematic Approach. Springer, Berlin, Germany.
Riestenpatt gen. Richter, M. and Rudolph, S. (2019). A
scientific discourse on creativity and innovation in the
formal context of graph-based design languages. In
13th Anniversary “Heron Island” Conference Work-
shop on Computational and Cognitive Models of Cre-
ative Design, (HI‘19), pages 1–19.
Rudolph, S. (2011). On design process modelling aspects
in complex systems. In 13th NASA-ESA Workshop
on Product Data Exchange (PDE 2011), pages 1–28,
Cypress, California, USA. National Aeronautics and
Space Administration.
Rudolph, S. (2023). Digital continuity, consistency and
interoperability along the product life-cycle using
graph-based design languages. In Global Product
Data Interoperability Summit (GPDIS 2023), pages
1–24, Phoenix, Arizona, USA. GPDIS.
Sahni, S. and Bhatt, A. (1980). The complexity of de-
sign automation problems. In Proceedings of the
17th Design Automation Conference, DAC ’80, page
402–411, New York, NY, USA. Association for Com-
puting Machinery.
Schmidt, J. and Rudolph, S. (2016). Automation opportu-
nities in the conceptual design of satellite propulsion
systems. In Systems Engineering and Concurrent En-
gineering for Space Applications (SECESA), pages 1–
8, Nordwijk, Netherlands. European Space Agency.
Schopper, C. (2023). Generative Layout- und Packingver-
fahren im digitalen Produktentwurf (in German). PhD
Thesis, University of Stuttgart.
Simon, H. A. (1969). The Sciences of the Artificial. MIT
Press, Cambridge, MA.
Voss, C., Petzold, F., and Rudolph, S. (2023). Graph trans-
formation in engineering design: an overview of the
last decade. Artificial Intelligence for Engineering De-
sign, Analysis and Manufacturing, 37:1–17.
Walter, B., Kaiser, D., and Rudolph, S. (2018). Machine-
executable model-based systems engineering with
graph-based design languages. In Bonjour, E., Krob,
D., Palladino, L., and Stephan, F., editors, Com-
plex Systems Design & Management, pages 203–210,
Cham. Springer International Publishing.
Walter, B., Kaiser, D., and Rudolph, S. (2019). From
manual to machine-executable model-based systems
engineering via graph-based design languages. In
Proceedings of the 7th International Conference on
Model-Driven Engineering and Software Develop-
ment, MODELSWARD 2019, page 201–208.
On Some Artificial Intelligence Methods in the V-Model of Model-Based Systems Engineering
393