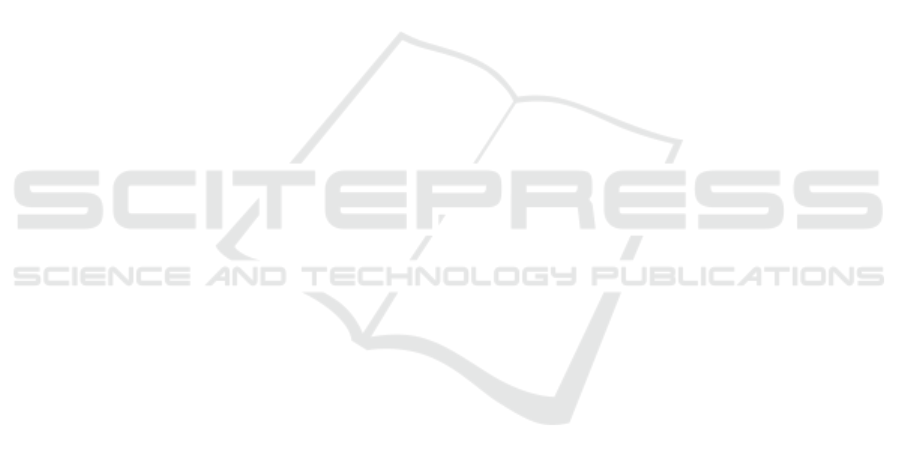
ent models could be made to determine the best. If
paired with physical tests, model parameters can be
changed in the CFD software and the resulting flow
can be compared to real observation in order to deter-
mine which model parameters reflect reality the best.
This possibility is the basis of a digital twin that is
currently being developed at KIT. The digital twin
is supposed to accompany the AoD printing proce-
dure featured in this paper. The AoD printhead repre-
sents a complex problem with many interactions that
are not sufficiently describable by established theo-
ries. The method presented in this paper can help to
develop empirical models in a semi-automated way.
While human supervision is still necessary, the work-
load is greatly reduced. Another possibility is that a
human can root the automatically generated empiri-
cal models through established theory and push the
understanding of the corresponding field forwards.
Another possibility for this method is the model
reduction. Only one simple type of mathematical
model has been examined in this paper. However, it
is possible to try several different mathematical model
reductions of complex problems and see which reduc-
tion does the best at emulating the complex interac-
tion. This would result in computationally cheaper
correlations which lessens the calculational load of a
digital twin.
The main advantage of this method is the adapt-
ability. The ELN provides a good structure for or-
derly and automated data storage. As long as the
simulation software of interest supports scripted pro-
cesses through an API, the procedure can be adapted.
The setup of this method is labor-intensive based on
the scope of what it is adapted to as all options for
parametrization need to be coded in. This effort is
also heavily dependent on the quality and flexibility
of the API of the simulation program. This makes it
suitable for larger or long-term applications such as a
digital twin where the overhead cost of programming
is smaller compared to the work that is saved through-
out the lifespan of the model.
ACKNOWLEDGEMENTS
The mesh independence study as well as the deter-
mining of the Rosin Rammler distribution values were
done by Tim Walter who we thank for his contribu-
tions.
The authors confirm that no artificial intelligence
(AI) was used in generating the text of this article.
REFERENCES
ANSYS, Inc. (2023a). Ansys Fluent Theory Guide. AN-
SYS, Inc., release 2023 r1 edition.
ANSYS, Inc. (2023b). Ansys Fluent User’s Guide. ANSYS,
Inc., release 2023 r1 edition.
Baby, T. T., Marques, G. C., Neuper, F., Singaraju, S. A.,
Garlapati, S., von Seggern, F., Kruk, R., Dasgupta, S.,
Sykora, B., Breitung, B., Sukkurji, P. A., Bog, U., Ku-
mar, R., Fuchs, H., Reinheimer, T., Mikolajek, M.,
Binder, J. R., Hirtz, M., Ungerer, M., Koker, L., Gen-
genbach, U., Mishra, N., Gruber, P., Tahoori, M., Hag-
mann, J. A., von Seggern, H., and Hahn, H. (2020). Print-
ing technologies for integration of electronic devices and
sensors. In Sidorenko, A. and Hahn, H., editors, Func-
tional Nanostructures and Sensors for CBRN Defence
and Environmental Safety and Security, NATO Science
for Peace and Security Series C: Environmental Security,
pages 1–34. Springer Netherlands, Dordrecht.
Brandt, N., Griem, L., Herrmann, C., Schoof, E.,
Tosato, G., Zhao, Y., Zschumme, P., and Selzer,
M. (2021). Kadi4mat: A research data infrastruc-
ture for materials science. Data Science Journal,
20:8. https://datascience.codata.org/articles/10.5334/dsj-
2021-008.
Choi, H. W., Zhou, T., Singh, M., and Jabbour, G. E. (2015).
Recent developments and directions in printed nanoma-
terials. Nanoscale, 7(8):3338–3355.
Cui, Z., editor (2016). Printed electronics: Materials, tech-
nologies and applications. John Wiley & Sons, Higher
Education Press, Singapore, 1st edition.
Gengenbach, U., Ungerer, M., Aytac, E., Koker, L., Re-
ichert, K.-M., Stiller, P., and Hagenmeyer, V. (2018).
An integrated workflow to automatically fabricate flexi-
ble electronics by functional printing and smt component
mounting. In Vogel-Heuser, B. and Lennartson, B., ed-
itors, Proc. 14th IEEE International Conference on Au-
tomation Science and Engineering (CASE), pages 1624–
1629.
IDS Inc. (2024). Nanojet aerosol print technology. https:
//www.idsnm.com/. Last accessed on Feb. 12, 2024.
IDTechEx Ltd. (2022). 3d electronics/additive electron-
ics 2022-2032: 3d printed electronics, molded intercon-
nect devices, in-mold electronics, aerosol jet, 3d metal-
lization, laser direct structuring, additively manufactured
electronics. sample pages. https://www.idtechex.com/e
n/research-report/3d-electronics-additive-electronics-2
022-2032/860. Last accessed on Feb. 12, 2024.
Magdassi, S., editor (2010). The chemistry of inkjet inks.
World Scientific Publishing, Singapore.
Menter, F. R. (1994). Two-equation eddy-ciscosity turbu-
lence models for engineering applications. AIAA Jour-
nal, 32(8):1598–1605.
Optomec Inc. (2024). Aerosol jet technology. https://opto
mec.com/printed-electronics/aerosol-jet-technology/.
Last accessed on Feb. 12, 2024.
Sieber, I., Thelen, R., and Gengenbach, U. (2020a). Assess-
ment of high-resolution 3d printed optics for the use case
of rotation optics. Optics express, 28(9):13423–13431.
Sieber, I., Thelen, R., and Gengenbach, U. (2020b). En-
hancement of high-resolution 3d inkjet-printing of op-
SIMULTECH 2024 - 14th International Conference on Simulation and Modeling Methodologies, Technologies and Applications
78