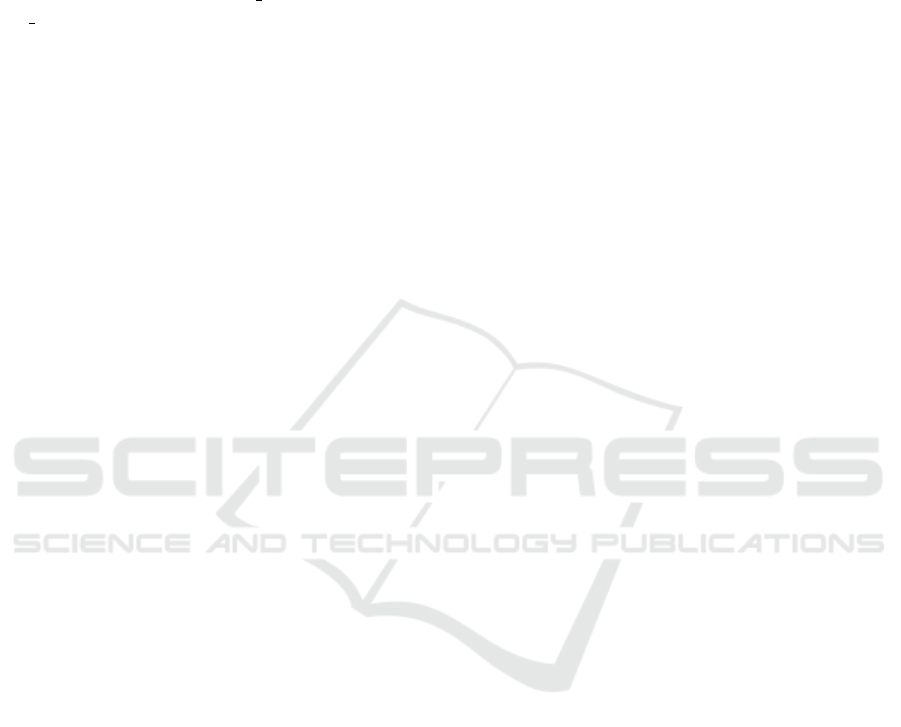
As a result, ABC variant (2) performs consistently
well across different cases, highlighting its versatility.
These findings underline the importance of balancing
stability and adaptability in algorithm design for ef-
fective scheduling in complex manufacturing settings.
Further research could explore different parameters of
ABC variant (2), including look ahead and emphasiz-
ing coef. Furthermore, the role and effectiveness of
scout bees in the system can be investigated.
ACKNOWLEDGEMENT
This work was performed in the course of project
SwarmIn supported by FFG under contract number
894072.
REFERENCES
Alvarado-Iniesta, A., Garcia-Alcaraz, J. L., Rodriguez-
Borbon, M. I., and Maldonado, A. (2013). Optimiza-
tion of the material flow in a manufacturing plant by
use of artificial bee colony algorithm. Expert Systems
with Applications, 40(12):4785–4790.
Gao, K., Cao, Z., Zhang, L., Chen, Z., Han, Y., and
Pan, Q. (2019). A review on swarm intelligence and
evolutionary algorithms for solving flexible job shop
scheduling problems. IEEE/CAA Journal of Automat-
ica Sinica, 6(4):904–916.
Gao, K. Z., Suganthan, P. N., Pan, Q. K., Tasgetiren, M. F.,
and Sadollah, A. (2016). Artificial bee colony algo-
rithm for scheduling and rescheduling fuzzy flexible
job shop problem with new job insertion. Knowledge-
based systems, 109:1–16.
Gupta, M. and Sharma, G. (2012). An efficient modified ar-
tificial bee colony algorithm for job scheduling prob-
lem. International Journal of Soft Computing and En-
gineering (IJSCE), 1(6).
Han, Y.-Y., Pan, Q.-K., Li, J.-Q., and Sang, H.-y. (2012).
An improved artificial bee colony algorithm for the
blocking flowshop scheduling problem. The Interna-
tional Journal of Advanced Manufacturing Technol-
ogy, 60(9-12):1149–1159.
Karaboga, D. and Basturk, B. (2007). A powerful and ef-
ficient algorithm for numerical function optimization:
artificial bee colony (abc) algorithm. Journal of global
optimization, 39(3):459–471.
Karaboga, D., Gorkemli, B., Ozturk, C., and Karaboga, N.
(2014). A comprehensive survey: artificial bee colony
(abc) algorithm and applications. Artificial Intelli-
gence Review, 42(1):21–57.
Khader, A. T., Al-betar, M. A., and Mohammed, A. A.
(2013). Artificial bee colony algorithm, its variants
and applications: a survey. Journal of Theoretical and
Applied Information Technology, 47(2):434–459.
Khatmi, E., Elmenreich, W., Wogatai, K., Schranz, M., Um-
lauft, M., Laure, W., and Wuttei, A. (2019). Swarm in-
telligence layer to control autonomous agents (swilt).
In STAF (Co-Located Events), pages 91–96.
Kumar, S., Sharma, V. K., and Kumari, R. (2014). A
novel hybrid crossover based artificial bee colony al-
gorithm for optimization problem. arXiv preprint
arXiv:1407.5574.
Lawler, E. L., Lenstra, J. K., Kan, A. H. R., and Shmoys,
D. B. (1993). Sequencing and scheduling: Algorithms
and complexity. Handbooks in Operations Research
and Management Science, 4:445–522.
Schranz, M., Di Caro, G. A., Schmickl, T., Elmenreich, W.,
Arvin, F., S¸ekercio
˘
glu, A., and Sende, M. (2021a).
Swarm intelligence and cyber-physical systems: con-
cepts, challenges and future trends. Swarm and Evo-
lutionary Computation, 60:100762.
Schranz, M., Umlauft, M., and Elmenreich, W. (2021b).
Bottom-up job shop scheduling with swarm intelli-
gence in large production plants. In Proceedings of
the 11th International Conference on Simulation and
Modeling, Methodolgies, Technologies and Applica-
tions (SIMULTECH), pages 327–334.
Sharma, N., Sharma, H., and Sharma, A. (2018). Beer froth
artificial bee colony algorithm for job-shop scheduling
problem. Applied Soft Computing, 68:507–524.
Umlauft, M., Gojkovic, M., Harshina, K., Majbour, K.,
and Schranz, M. (2023a). Bees, bats and glow-
worms: Swarm algorithms for optimizing industrial
plants from the bottom-up. In International Confer-
ence on Agents and Artificial Intelligence, pages 3–25.
Springer.
Umlauft, M., Gojkovic, M., Harshina, K., and Schranz, M.
(2023b). Bottom-up bio-inspired algorithms for opti-
mizing industrial plants. In International Conference
on Agents and Artificial Intelligence (ICAART), pages
59–70.
Umlauft, M., Schranz, M., and Elmenreich, W. (2022).
Simulation of swarm intelligence for flexible job-shop
scheduling with swarmfabsim: Case studies with arti-
ficial hormones and an ant algorithm. In International
Conference on Simulation and Modeling Methodolo-
gies, Technologies and Applications, pages 133–155.
Springer.
Yao, B. Z., Yang, C. Y., Hu, J. J., Yin, G. D., and Yu, B.
(2010). An improved artificial bee colony algorithm
for job shop problem. In Applied Mechanics and Ma-
terials, volume 26, pages 657–660. Trans Tech Publ.
Yurtkuran, A. and Emel, E. (2014). A modified artificial bee
colony algorithm for-center problems. The Scientific
World Journal, 2014.
Zhang, G., Shao, X., Li, P., and Gao, L. (2009). An effec-
tive hybrid particle swarm optimization algorithm for
multi-objective flexible job-shop scheduling problem.
Computers & Industrial Engineering, 56(4):1309–
1318.
Artificial Bee Colony Algorithm: Bottom-Up Variants for the Job-Shop Scheduling Problem
111