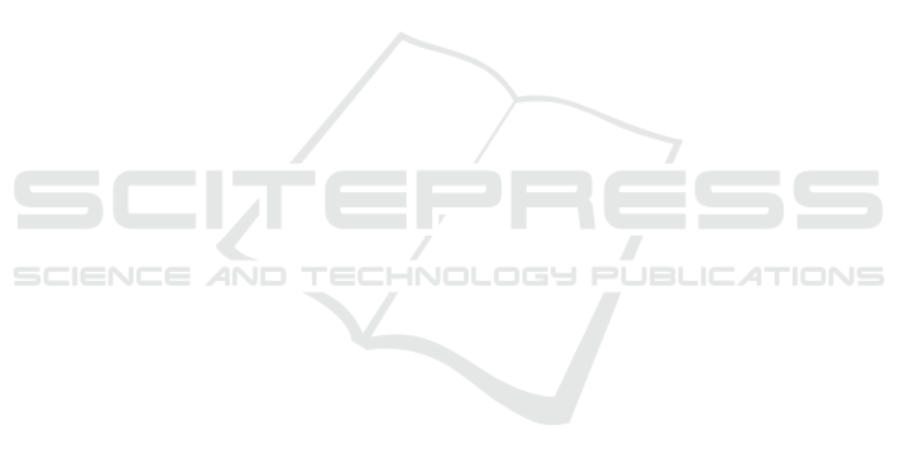
Marler, R. T. and Arora, J. S. (2005). Function-
transformation methods for multi-objective optimiza-
tion. Engineering Optimization, 37(6):551–570.
Miettinen, K. (2012). Nonlinear multiobjective optimiza-
tion, volume 12. Springer Science & Business Media.
¨
Ozdemir, D., Deliktas¸, D., and Ermutaf, E. G. (2022).
A decision support system for multi-objective porce-
lain container loading problem based on genetic algo-
rithm. Academic Platform Journal of Engineering and
Smart Systems, 10(2):78–85.
Panchal, G. and Panchal, D. (2015). Solving np hard prob-
lems using genetic algorithm. Transportation, 106:6–
2.
Paquay, C., Schyns, M., and Limbourg, S. (2016). A
mixed integer programming formulation for the three-
dimensional bin packing problem deriving from an air
cargo application. International Transactions in Op-
erational Research, 23(1-2):187–213.
Ramos, A. G., Silva, E., and Oliveira, J. F. (2018). A new
load balance methodology for container loading prob-
lem in road transportation. European Journal of Op-
erational Research, 266(3):1140–1152.
Rom
˜
ao, O. C., dos Santos, A. G., and Arroyo, J. E. C.
(2012). A two phase hybrid method to support 2d
and 3d vehicle loading. In 2012 12th International
Conference on Intelligent Systems Design and Appli-
cations (ISDA), pages 320–325. IEEE.
Ruiz, R., Maroto, C., and Alcaraz, J. (2006). Two new ro-
bust genetic algorithms for the flowshop scheduling
problem. Omega, 34(5):461–476.
Sheng, L., Hongxia, Z., Xisong, D., and Changjian, C.
(2016). A heuristic algorithm for container loading
of pallets with infill boxes. European Journal of Op-
erational Research, 252(3):728–736.
Silva, E., Oliveira, J. F., and W
¨
ascher, G. (2016). The
pallet loading problem: a review of solution methods
and computational experiments. International Trans-
actions in Operational Research, 23(1-2):147–172.
Terno, J., Scheithauer, G., Sommerweiß, U., and Riehme,
J. (2000). An efficient approach for the multi-pallet
loading problem. European Journal of Operational
Research, 123(2):372–381.
Tian, T., Zhu, W., Lim, A., and Wei, L. (2016). The multiple
container loading problem with preference. European
Journal of Operational Research, 248(1):84–94.
Toffolo, T. A., Esprit, E., Wauters, T., and Berghe, G. V.
(2017). A two-dimensional heuristic decomposition
approach to a three-dimensional multiple container
loading problem. European Journal of Operational
Research, 257(2):526–538.
V
´
elez-Gallego, M. C., Teran-Somohano, A., and Smith,
A. E. (2020). Minimizing late deliveries in a truck
loading problem. European Journal of Operational
Research, 286(3):919–928.
W
¨
ascher, G., Haußner, H., and Schumann, H. (2007).
An improved typology of cutting and packing prob-
lems. European journal of operational research,
183(3):1109–1130.
Wu, Y., Li, W., Goh, M., and De Souza, R. (2010). Three-
dimensional bin packing problem with variable bin
height. European journal of operational research,
202(2):347–355.
Young-Gun, G. and Kang, M.-K. (2001). A fast algorithm
for two-dimensional pallet loading problems of large
size. European Journal of Operational Research,
134(1):193–202.
Y
¨
uceer,
¨
U. and
¨
Ozakc¸a, A. (2010). A truck load-
ing problem. Computers & Industrial Engineering,
58(4):766–773.
Zhang, D.-F., Peng, Y., Zhu, W.-X., and Chen, H.-W.
(2009). A hybrid simulated annealing algorithm
for the three-dimensional packing problem. Chinese
Journal of Computers, 32(11):2147–2156.
Zheng, J.-N., Chien, C.-F., and Gen, M. (2015). Multi-
objective multi-population biased random-key genetic
algorithm for the 3-d container loading problem.
Computers & Industrial Engineering, 89:80–87.
Zhou, Q. and Liu, X. (2017). A swarm optimization al-
gorithm for practical container loading problem. In
IECON 2017-43rd Annual Conference of the IEEE In-
dustrial Electronics Society, pages 5690–5695. IEEE.
Optimisation of Ceramic Kiln Loading Problem Using Multi-Objective Genetic Algorithm
255