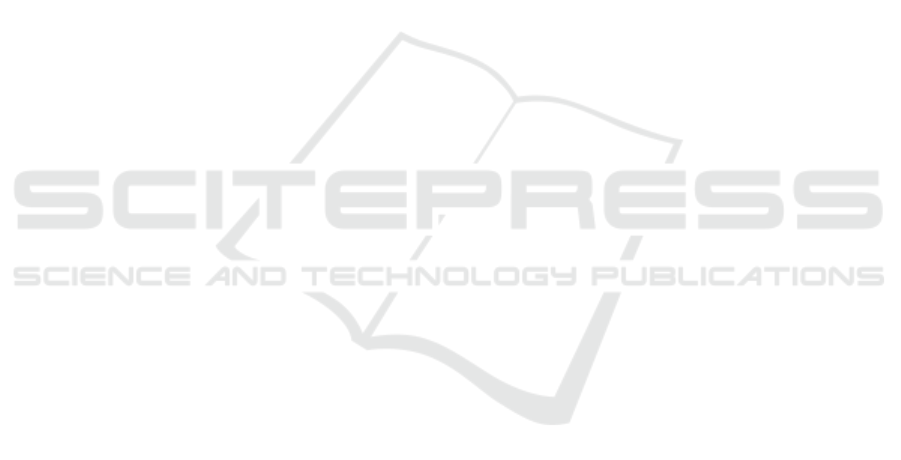
capability to easily incorporate inequality constraints
on variables, including both upper and lower bounds
on inputs or outputs (Darby and Nikolaou, 2012).
There is a considerable volume of literature re-
garding the application of MPC to HVAC systems
(Taheri et al., 2024a; Saletti et al., 2020; Yao and
Shekhar, 2021a). However, none of previous works
yet offered a comprehensive platform in this con-
text, capable of dealing with the different operational
modes typical of HVAC systems (e.g., heating, cool-
ing, and defrost).
In this paper, we aim to develop a switching event-
triggered model predictive control for HVAC systems,
which reacts to external events to switch between dif-
ferent modalities. We implement and evaluate the
approach on an industrial real system, which uses
legacy control software. We begin by processing the
data acquired from HVAC machines during field tests,
which involves standardizing formats, applying filter-
ing methods, resampling, and performing data inter-
polation. We then develop a model of the dynamical
behaviour used to design a multi-variable controller.
We use standard system identification techniques to
create a model from the data in different modalities.
We then design the switching MPC, thus an MPC for
different modalities and a switch logic with a state
machine that activates the various controllers. Finally,
we focus on validating the effectiveness of the model
as well as switching MPC methodology. This step
includes both the validation of the identified models
in the different modalities as well as the evaluation
of the system’s switching behaviour under simulated
conditions.
The organization of the current manuscript is as
follows. In section 2, the related works are given. In
section 3.1 the problem is described in more detail. In
the next sections, the model, data acquisition and sys-
tem identification and successively the switching con-
trol approach implementation, are presented respec-
tively. The results are given in section 6, and eventu-
ally, conclusive remarks are presented in the last sec-
tion.
2 RELATED WORKS
In (Afroz et al., 2018), various modeling techniques
used in HVAC systems are studied, assessing their ap-
plicability, strengths, and weaknesses, together with
their impact on energy efficiency and indoor environ-
mental quality. The existing gaps are highlighted, and
various recommendations to enhance the performance
of building HVAC systems are given. In (Taheri et al.,
2024b), it is demonstrated through simulation that the
Model Predictive Control (MPC) approach provides
a 7% greater reduction in energy consumption com-
pared to the classical PID method when applied to
HVAC systems in commercial buildings. In (Staino
et al., 2016), two different optimization scenarios
(selfish and cooperative) are focused on the analy-
sis of the performance of MPC in the heat pumps of
buildings.
Saletti et al. proposed a novel control methodol-
ogy using MPC for district heating networks, aimed
at optimizing thermal energy distribution to build-
ings using a new optimization algorithm (Saletti et al.,
2020). It is demonstrated that it gives significant re-
ductions in energy consumption and improved indoor
comfort, compared to conventional controllers. How-
ever, it is based on a linearized approximated model
that does not always reflect the real characteristics of
the system.
In (Yao and Shekhar, 2021b), a comprehensive
analysis has been conducted in terms of implemen-
tation, optimization, application, and modeling, as
well as the overall scheme in the context of MPC for
HVAC systems. However, the need for a more real-
istic model that predicts the outlet thermal water dy-
namics has not yet been met. Additional work is re-
quired to achieve optimized output control and to pro-
vide an improved dynamical behavior for the MPC
controller. Specifically, for HVAC systems, the need
to switch in real-time between MPC controllers has
received only limited attention in the literature. It is
concluded that the application of MPC in the HVAC
field remains a wide-open subject, with much work
still to be done.
3 SYSTEM DESCRIPTION
In this section, we give a high-level description of the
problem context and the specific use case under con-
sideration. In the following sub-section, we focus on
the system characterization.
3.1 Problem Description
Our objective is to re-design with a model-based ap-
proach the control of real industrial heat pumps that
are already in operation and that we can test to col-
lect data. In particular, The tested heat pump units
come in a range of power capacity sizes to suit dif-
ferent needs, ranging from 5 kW to 15 kW nominal
capacities. These units offer various installation op-
tions to accommodate different space and aesthetic
requirements. The installation options include tradi-
tional setups, vertical and horizontal outlet configu-
ICINCO 2024 - 21st International Conference on Informatics in Control, Automation and Robotics
38