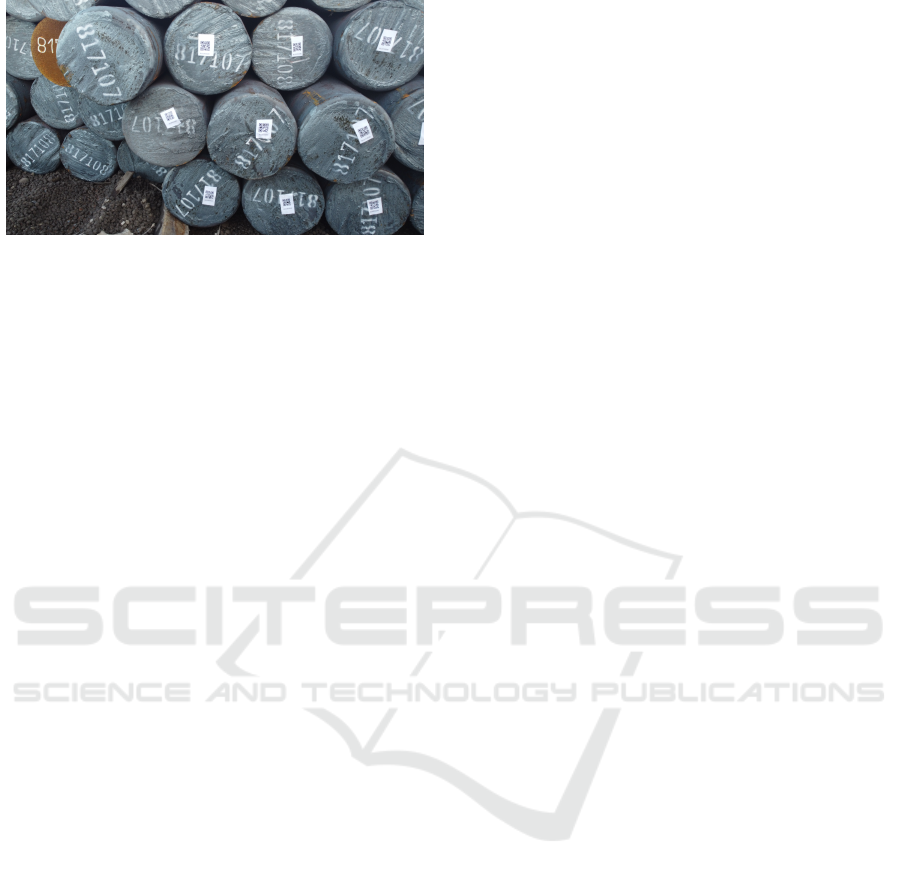
Figure 1: Illustration of the products position with QRcode
tags.
in inventory management, intra-logistics, and surveil-
lance in smart warehouses.
However, a critical challenge persists in ensuring
uninterrupted drone tracking and accurate product po-
sition inference. Existing techniques often rely on
fixed infrastructure or external markers, unsuitable for
agile and rapidly changing environments like outdoor
storage yards or manufacturing facilities, as explained
in our case.
In this paper, we present a novel system for rela-
tive positioning utilizing images captured by drones.
This system represents a fundamental change in prod-
uct positioning, as it calculates item locations relative
to one another, rather than depending on fixed points
or external infrastructure. By doing so, it establishes
a precise mechanism to automatically identify prod-
ucts’ locations for autonomous warehouse manage-
ment operations. Our method offers an increased ac-
curacy and efficiency within complex industrial en-
vironments. Specifically for environments such as
warehouses and manufacturing floors, where conven-
tional systems often fall short in providing accurate
and reliable information, our approach stands out for
its adaptability without the need for exterior mark-
ers or infrastructure and shows a outstanding perfor-
mance.
The remainder of this paper is organized as fol-
lows: Section 2 reviews the related work on sys-
tem positioning. Section 3 describes the proposed
framework, as well as the main concepts involved in
this work. Implementation and empirical results of
the proposed system are detailed in Section 4, while
Section 5 summarizes our contributions and sketches
some of our future perspectives.
2 STATE OF THE ART
The PILOT system, as detailed in (Famili et al.,
2023), is an in indoor drone localization through its
utilization of Time of Arrival (ToA) analysis of ultra-
sound signals. This approach tackles the complexity
of indoor environments, such as the multi-path fad-
ing. Moreover, the integration of Frequency Hopping
Spread Spectrum (FHSS) technology showcases in-
novative strategies to enhance location estimation ac-
curacy, although specific precision metrics are not ex-
plicitly outlined in the literature.
In outdoor environments, the fusion of the Global
Navigation Satellite System (GNSS) with compass-
based systems, as highlighted by Flavia et al. in
(Causa and Fasano, 2021), has markedly enhanced
autonomous drone navigation. Although GNSS-
based approaches have gained precision improve-
ments, they may still lack in accuracy for locating
products stored in densely packed piles.
The employment of stereo vision techniques for
indoor drone control, as elucidated by Anand et al. in
(George et al., 2023), represents a significant stride
in indoor positioning systems. This method empha-
sizes 3D reconstruction through drone-mounted cam-
eras, boasting high positional accuracy, especially in
aligning the drone’s yaw rotation with the virtual cam-
era. However, precise precision figures remain absent
from existing summaries.
Other approaches, such as Sensor Fusion, in-
tegrate ultrasound, LIDAR Time of Flight (ToF)
rangefinders, visual odometers, and Ultra-Wide Band
(UWB) positioning (Xu et al., 2018), promising ap-
proximately 5 cm accuracy during flight.
Furthermore, UWB Sensing for Indoor Preci-
sion introduces a system employing impulse-radio
ultra-wideband (IR-UWB) two-way ranging (TWR),
achieving high precision and interference resilience.
With a reported standard deviation of 1.2 cm for
single-measurement TWR in semi-closed environ-
ments, it holds particular significance for demanding
indoor applications.
Building upon these advancements, this paper in-
troduces a new approach for autonomous warehouse
management, focusing on accurately identifying the
relative positions of products items in dynamic out-
door environments. By combining drone-based image
capture with a high-speed processing algorithm sup-
ported by a trustworthiness score, this system ensures
precise identification of each item’s location. Addi-
tionally, it provides a user-friendly visualization inter-
face to facilitate product localization in outdoor ware-
houses.
ICINCO 2024 - 21st International Conference on Informatics in Control, Automation and Robotics
358