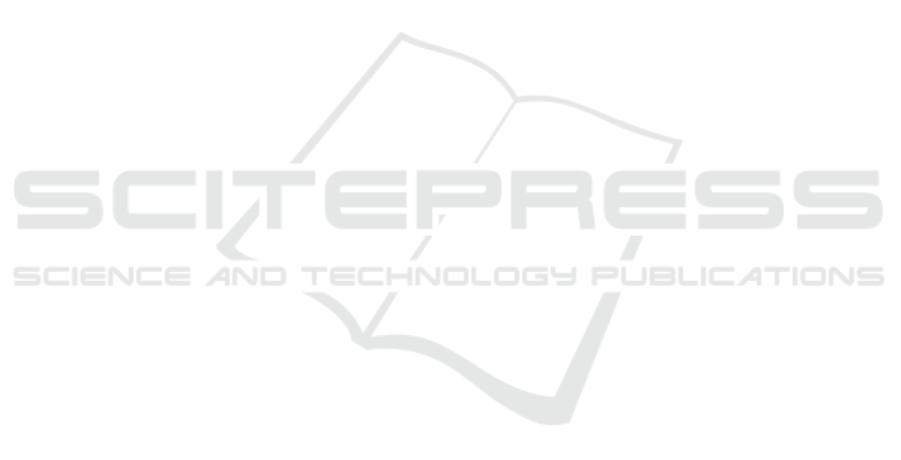
5 PREDICTION OF DYEING
NON-CONFORMITIES
FACTORS
This section explores the use of machine learning al-
gorithms, specifically RF and GBT, to predict key fac-
tors that may contribute to non-conformities and ex-
tract feature importance, identifying the most signifi-
cant factors contributing to these issues. Understand-
ing these key features enables targeted interventions
and process optimizations, enhancing product quality
and reducing defect rates.
RF combines multiple decision trees to enhance
predictive accuracy and control overfitting, making it
suitable for datasets with numerous features and non-
linear relationships (Robnik-Sikonja, 2004). This al-
gorithm has been effectively utilized in various indus-
trial contexts, such as predictive maintenance, where
it anticipates equipment failures by analyzing sen-
sor data and operational logs, thus minimizing down-
time and improving productivity (Kusiak and Verma,
2011). Additionally, RF provides insights into fea-
ture importance, crucial for understanding key fac-
tors influencing non-conformities in dyeing processes
(Breiman, 2001).
Conversely, the GBT algorithm builds trees se-
quentially, with each new tree correcting errors made
by the previous ones, thereby significantly enhancing
prediction accuracy (Friedman, 2001). GBTs have
demonstrated superior performance in industrial ap-
plications and in manufacturing. GBTs optimize pro-
duction processes by identifying critical factors influ-
encing product quality, enabling precise control and
reduction of non-conformities (He and Wu, 2018).
5.1 Findings of the Random Forest
Model
The Figure 2 shows a representative tree model ob-
tained using the RF algorithm (Ho, 1995). The model
configuration chosen was: the number of trees in the
forest equals to 100 and the minimum number of sam-
ples required in leaf node equals to 50 and the data
was divided into 80% for training and 20% for test-
ing. The returned RF model represented in the Fig-
ure shows the factors that lead to non-conformities,
which was used as classe label. According to the
root node, the most important factor is ‘Poorly anal-
ysed’ processes mainly resulting in ‘Failed’ classifi-
cations. After a thorough analysis, the next signifi-
cant factor is the ‘Dyed (folded) accessory along with
mesh’ process, frequently leading to ‘Undyed’ non-
conformities. Next, there are machine-specific fac-
tors, especially those involving the colouring machine
‘TNJT25’ and ‘TNJT23’, as well as fabric-related is-
sues like problems with ‘Golves’ fabric, play a signif-
icant role in influencing non-conformities. In the Fig-
ure, it also possible to see that ‘Colourless’ colourants
and ‘Piquet’ fabrics play a major role in ‘Other’ non-
conformities. In addition, issues related to the dye-
ing process such as ‘Process phases in different con-
ditions’ and ‘Insufficient dispossal by normal process’
are important elements.
The obtained RF estimator’s performance mea-
sures shows the model’s accuracy in predicting dif-
ferent types of non-conformities. The precision for
predicting the non-conformity ‘Crease’ is 0.53, which
means that 53% of the predicted creases were correct.
The recall is 0.23, suggesting that only 23% of the ac-
tual creases were identified. The f1-score is 0.33, re-
flecting the balance between precision and recall. The
‘Failed’ non-conformity has perfect precision (1.00)
and high recall (0.87), resulting in a high f1-score
(0.93), which means that 100% of ‘Failed’ predictions
are accurate. The precision and recall in the ‘Oil’
non-conformity are both very high (0.97 and 0.99,
respectively) and a f1-score of 0.98. The ‘Stained’
non-conformity has a precision of 0.60 and a recall of
0.88. The precision is 0.92 and the recall is 0.81 on
the ‘Undyed’ non-conformity, resulting in an f1-score
of 0.86. In the ‘Other’ non-conformity the precision
is 0.54 and the recall is 0.73, resulting in an f1-score
of 0.62. The overall accuracy of the model is 0.79,
so it shows that almost 80% of the predictions are ac-
curate. This is a strong performance, indicating that
the model is successful in identifying various types of
non-conformities.
With the analysis of important features from the
RF model one can know which are the features
that impact mostly the non-conformities appearances.
The cause ‘Poorly analysed’ remains the most in-
fluential feature of non-conformities, with an impor-
tance value of 0.385060. The second most influ-
ential feature is the cause ‘Process phases in dif-
ferent conditions’ which presents an importance of
0.141318. The cause ‘Insufficient disposal by nor-
mal process’, rated at 0.135305 in terms of impor-
tance, is the third most influential feature. The cause
‘Poorly executed/monitored process’, with a signif-
icance rating of 0.117062, is also a major factor in
non-conformities.
Additional important factors are the ‘Other’
causes (0.052049), the cause ‘Lack of machine/cart
cleaning’ (0.049191) and the cause ‘Process inter-
rupted for review’ (0.042287). While not as influ-
ential enough as the other main causes, these factors
still greatly affect non-conformities. Other process
problems like the cause ‘Dyed (folded) accessory to-
Enhancing Dyeing Processes with Machine Learning: Strategies for Reducing Textile Non-Conformities
367