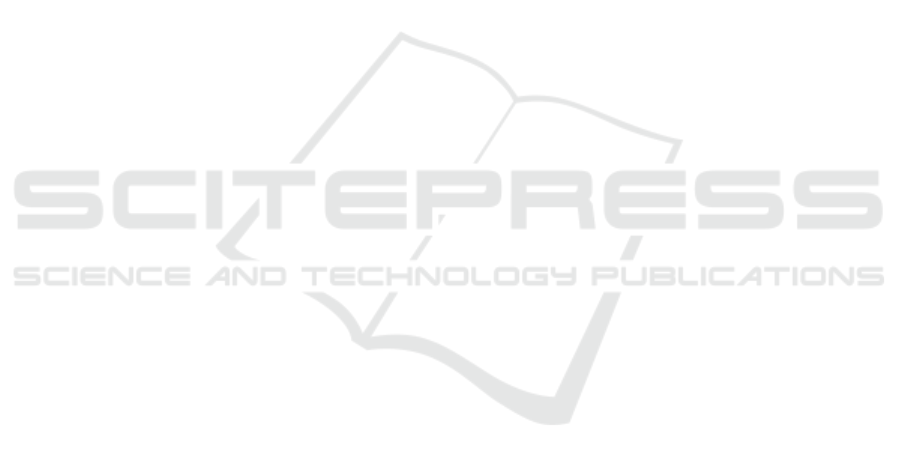
eration and synchronization of robotic tasks. Our ap-
proach is fully in line with Industry 4.0, using tech-
nologies such as the OPC UA protocol, which enables
interoperability and using machine vision with image
processing. In fact, by centralizing all the data re-
quired to perform the tasks of each robot, the digital
twin can reconstruct the working area and thus con-
trol each robot even if this last has a faulty sensor.
Moreover, thanks to the knowledge of this working
environment, the movement of each robot arm is min-
imized, thus reducing energy consumption and me-
chanical wear.
Future research will focus on developing a
decision-making layer in the digital twin, which will
be responsible for planning robot tasks and optimis-
ing image processing. In our case study, the robots
receive the position of the parts to be picked and au-
tonomously choose which one to pick. The decision-
making layer currently under development will in-
dicate the most efficient sequence of movements for
each robotic arm, to save even more time and energy.
ACKNOWLEDGEMENTS
The project was supported in part by Appel
`
a manifes-
tation d’int
´
er
ˆ
et (AMI) du R
´
eseau d’ESR du site Cham-
pardennais.
REFERENCES
Bajic, B., Rikalovic, A., Suzic, N., and Piuri, V. (2021).
Industry 4.0 implementation challenges and opportu-
nities: A managerial perspective. IEEE Systems Jour-
nal, 15(1):546–559.
Bansal, R., Khanesar, M. A., and Branson, D. (2019).
Ant colony optimization algorithm for industrial robot
programming in a digital twin. In 2019 25th Inter-
national Conference on Automation and Computing
(ICAC), pages 1–5. IEEE.
Barenji, A. V., Liu, X., Guo, H., and Li, Z. (2021). A dig-
ital twin-driven approach towards smart manufactur-
ing: reduced energy consumption for a robotic cell.
International Journal of Computer Integrated Manu-
facturing, 34:844–859.
Barricelli, B. R., Casiraghi, E., and Fogli, D. (2019). A
survey on digital twin: Definitions, characteristics,
applications, and design implications. IEEE Access,
7:167653–167671.
Erkoyuncu, J. A., Butala, P., Roy, R., et al. (2018). Digital
twins: Understanding the added value of integrated
models for through-life engineering services. Proce-
dia Manufacturing, 16:139–146.
Kousi, N., Gkournelos, C., Aivaliotis, S., Giannoulis, C.,
Michalos, G., and Makris, S. (2019). Digital twin for
adaptation of robots’ behavior in flexible robotic as-
sembly lines. Procedia manufacturing, 28:121–126.
Liang, X., Xiao, R., and Zhang, J. (2022). A review on
digital twin for robotics in smart manufacturing. In
2022 IEEE 17th Conference on Industrial Electronics
and Applications (ICIEA), pages 1510–1515.
Liu, X., Jiang, D., Tao, B., Jiang, G., Sun, Y., Kong,
J., Tong, X., Zhao, G., and Chen, B. (2022). Ge-
netic algorithm-based trajectory optimization for dig-
ital twin robots. Frontiers in Bioengineering and
Biotechnology, 9:793782.
Matulis, M. and Harvey, C. (2021). A robot arm digital
twin utilising reinforcement learning. Computers &
Graphics, 95:106–114.
Mohammed, A., Schmidt, B., Wang, L., and Gao, L. (2014).
Minimizing energy consumption for robot arm move-
ment. Procedia CIRP, 25:400–405.
Niryo (2024). https://niryo.com/.
Profanter, S., Tekat, A., Dorofeev, K., Rickert, M., and
Knoll, A. (2019). Opc ua versus ros, dds, and mqtt:
Performance evaluation of industry 4.0 protocols. In
2019 IEEE International Conference on Industrial
Technology (ICIT), pages 955–962.
ProsysOPC (2024). https://prosysopc.com/.
Sow, M. C., Assila, A., Garcia, D., Martinez, S., Zghal,
M., and Baudry, D. (2023). Towards the development
of a digital twin for micro learning factory: A proof
of concept. In International Conference on Extended
Reality, pages 284–298. Springer.
Wanasinghe, T. R., Wroblewski, L., Petersen, B. K., Go-
sine, R. G., James, L. A., De Silva, O., Mann, G. K. I.,
and Warrian, P. J. (2020). Digital twin for the oil and
gas industry: Overview, research trends, opportuni-
ties, and challenges. IEEE Access, 8:104175–104197.
Webots (2024). https://cyberbotics.com/.
Wu, Z., Chen, S., Han, J., Zhang, S., Liang, J., and Yang,
X. (2022). A low-cost digital twin-driven positioning
error compensation method for industrial robotic arm.
IEEE Sensors Journal, 22(23):22885–22893.
Cooperation and Synchronization of Robotic Tasks Using a Digital Twin
79