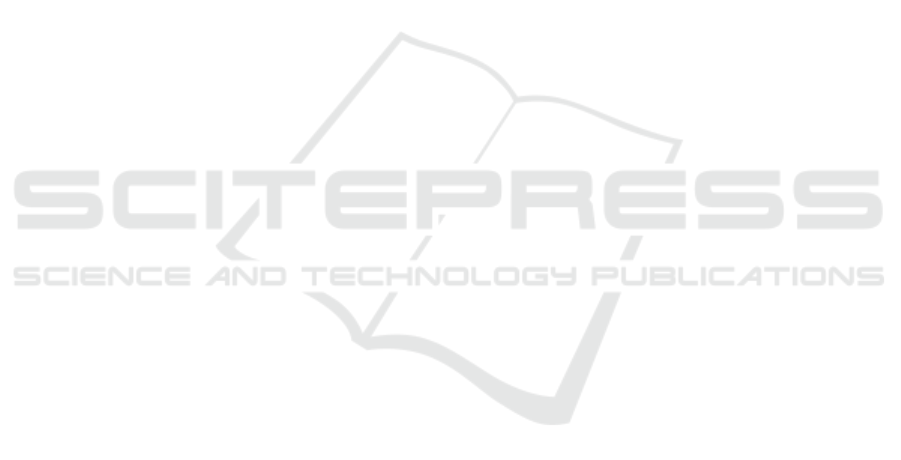
Hjorth, S. et al. (2022). Human–robot collaboration in in-
dustrial environments: A literature review on non-
destructive disassembly. Robotics and Computer-
Integrated Manufacturing, 73:102208.
Huang, J., Pham, D. T., Li, R., Qu, M., Wang, Y., Kerin,
M., Su, S., Ji, C., Mahomed, O., Khalil, R., et al.
(2021). An experimental human-robot collaborative
disassembly cell. Computers & Industrial Engineer-
ing, 155:107189.
Huang, J., Pham, D. T., Wang, Y., Ji, C., Xu, W., Liu, Q.,
and Zhou, Z. (2019). A strategy for human-robot col-
laboration in taking products apart for remanufacture.
Fme Transactions, 47(4):731–738.
Jungbluth, J., Gerke, W., and Plapper, P. (2017). An intelli-
gent agent-controlled and robot-based disassembly as-
sistant. In IOP Conf. Series: Materials Science and
Engineering, volume 235, page 012005. IOP Publish-
ing.
Lee, M.-L., Behdad, S., Liang, X., and Zheng, M. (2020a).
Disassembly sequence planning considering human-
robot collaboration. In 2020 American Control Con-
ference, pages 2438–2443. IEEE.
Lee, M.-L., Behdad, S., Liang, X., and Zheng, M. (2020b).
A real-time receding horizon sequence planner for dis-
assembly in a human-robot collaboration setting. In
Int. S. on Flexible Automation, volume 83617, page
V001T04A004. American Society of Mechanical En-
gineers.
Lee, M.-L., Behdad, S., Liang, X., and Zheng, M. (2022).
Task allocation and planning for product disassem-
bly with human–robot collaboration. Robotics and
Computer-Integrated Manufacturing, 76:102306.
Li, K., Liu, Q., Xu, W., Liu, J., Zhou, Z., and Feng, H.
(2019). Sequence planning considering human fatigue
for human-robot collaboration in disassembly. Proce-
dia CIRP, 83:95–104.
Liao, H.-y., Chen, Y., Hu, B., and Behdad, S. (2023).
Optimization-based disassembly sequence planning
under uncertainty for human–robot collaboration.
Journal of Mechanical Design, 145(2):022001.
Liu, W., Liang, X., and Zheng, M. (2023). Task-
constrained motion planning considering uncertainty-
informed human motion prediction for human–robot
collaborative disassembly. IEEE/ASME Transactions
on Mechatronics.
Liu, Z., Liu, Q., Xu, W., Liu, Z., Zhou, Z., and Chen,
J. (2019). Deep learning-based human motion pre-
diction considering context awareness for human-
robot collaboration in manufacturing. procedia cirp,
83:272–278.
Lou, S., Zhang, Y., Tan, R., and Lv, C. (2024). A human-
cyber-physical system enabled sequential disassem-
bly planning approach for a human-robot collabora-
tion cell in industry 5.0. Robotics and Computer-
Integrated Manufacturing, 87:102706.
Mateus, J. E. C., Aghezzaf, E.-H., Claeys, D., Lim
`
ere, V.,
and Cottyn, J. (2018). Method for transition from
manual assembly to human-robot collaborative as-
sembly. IFAC-PapersOnLine, 51(11):405–410.
Matsas, E. et al. (2017). Design of a virtual reality training
system for human–robot collaboration in manufactur-
ing tasks. Int. J. on Interactive Design and Manufac-
turing (IJIDeM), 11:139–153.
Pacaux-Lemoine, M.-P., Habib, L., and Carlson, T. (2023).
Levels of cooperation in human–machine systems: A
human–bci–robot example. Handbook of Human-
Machine Systems, pages 61–69.
Parsa, S. et al. (2021). Human-robot collaboration disas-
sembly planning for end-of-life product disassembly
process. Robotics and Computer-Integrated Manufac-
turing, 71:102170.
Prioli, J. P. J. and Rickli, J. L. (2020). Collaborative robot
based architecture to train flexible automated disas-
sembly systems for critical materials. Procedia Man-
ufacturing, 51:46–53.
Renteria, A. et al. (2019). Human-robot collaboration as a
new paradigm in circular economy for weee manage-
ment. Procedia Manufacturing, 38:375–382.
Sartori, A. and Schlette, C. (2021). Visual programming of
a human-machine interface for a multi-robot support
system. In 2021 4th IEEE Int. Conf. on ICPS, pages
387–392. IEEE.
Tian, S., Liang, X., and Zheng, M. (2023). An optimization-
based human behavior modeling and prediction for
human-robot collaborative disassembly. In 2023
American Control Conference, pages 3356–3361.
IEEE.
Vongbunyong, S., Vongseela, P., and Sreerattana-aporn, J.
(2017). A process demonstration platform for product
disassembly skills transfer. Procedia CIRP, 61:281–
286.
Wu, T., Zhang, Z., Zeng, Y., Zhang, Y., Guo, L., and
Liu, J. (2024). Techno-economic and environmen-
tal benefits-oriented human–robot collaborative disas-
sembly line balancing optimization in remanufactur-
ing. Robotics and Computer-Integrated Manufactur-
ing, 86:102650.
Xu, C., Wei, H., Guo, X., Liu, S., Qi, L., and Zhao, Z.
(2020a). Human-robot collaboration multi-objective
disassembly line balancing subject to task failure via
multi-objective artificial bee colony algorithm. IFAC-
PapersOnLine, 53(5):1–6.
Xu, W., Tang, Q., Liu, J., Liu, Z., Zhou, Z., and Pham, D. T.
(2020b). Disassembly sequence planning using dis-
crete bees algorithm for human-robot collaboration in
remanufacturing. Robotics and Computer-Integrated
Manufacturing, 62:101860.
Yuan, G., Liu, X., Zhang, C., Pham, D. T., and Li, Z. (2023).
A new heuristic algorithm based on multi-criteria re-
silience assessment of human–robot collaboration dis-
assembly for supporting spent lithium-ion battery re-
cycling. Engineering Applications of Artificial Intelli-
gence, 126:106878.
Human-Robot Cooperation in Disassembly: A Rapid Review
219