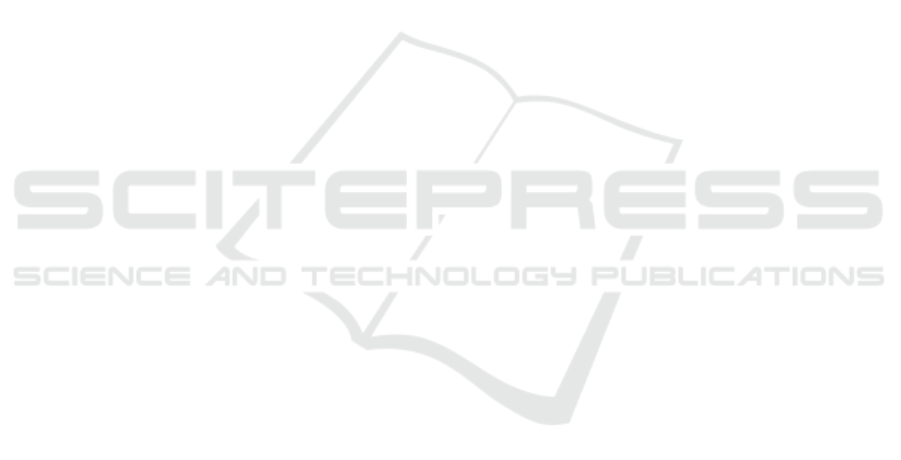
5 CONCLUSIONS
This study provides insight into the performance of
three adaptive control strategies under various condi-
tions when applied to a nonlinear process with vari-
able parameters and dominating delay. The tested
controllers used were Adaptive PID, Dual-Adaptive
PID, and Adaptive Gain FO-PID . The Adaptive Gain
FO-PID consistently minimized the ISE and main-
tained a low ISCO, contributing to the life of the fi-
nal control element with precise control and energy
efficiency.
Adaptive Gain FO-PID achieved rapid stabiliza-
tion with minimal overshoot and smooth disturbance
response, making it suitable for tight control and ro-
bustness. Conversely, the Dual-Adaptive PID con-
troller responded more aggressively to disturbances,
resulting in higher ISE and ISCO values, which can
be suitable for environments prioritizing quick adap-
tation but non-efficiency in energy. The Adaptive PID
controller balanced error minimization and control ef-
fort, making it suitable for moderate error reduction,
although its oscillations may limit effectiveness in dy-
namic or noise-sensitive environments.
These findings stress the importance of select-
ing the appropriate adaptive control strategy based
on application requirements, balancing error mini-
mization, energy efficiency, response time, and distur-
bance robustness. Therefore, the Adaptive Gain FO-
PID presents the best for precision and performance,
the Dual-Adaptive PID for rapid adaptation, and the
Adaptive PID for a balanced approach.
Despite their advantages in performance for iden-
tification and control, fractional-order controllers re-
quire further development for practical implementa-
tions. Implementing Adaptive Gain FO-PID con-
trollers involves fractional calculus, making them
challenging since transitioning to fractional order re-
quires advanced numerical methods, adding complex-
ity and computational overhead. The gap between
theory and practice should be reduced, and improve-
ments in the knowledge of fractional calculus should
be made so that plant operators can prove the advan-
tages over conventional PID solutions.
ACKNOWLEDGEMENTS
SV and MV thank the Advanced Control Systems Re-
search Group at USFQ for a research internship.
The Universidad San Francisco de Quito sup-
ported this work through the Poli-Grants Program un-
der Grant 24280.
REFERENCES
Anchitipan, E. and Camacho, O. (2021). Processes with
variable parameters and dominant time delay: a fuzzy
adaptive control approaches comparison. In Recent
Advances in Electrical Engineering, Electronics and
Energy: Proceedings of the CIT 2020 Volume 1, pages
181–195. Springer.
Annaswamy, A. M. and Fradkov, A. L. (2021). A historical
perspective of adaptive control and learning. Annual
Reviews in Control, 52:18–41.
˚
Astr
¨
om, K. J. and H
¨
agglund, T. (2006). Pid control. IEEE
Control Systems Magazine, 1066.
˚
Astr
¨
om, K. J., H
¨
agglund, T., and Astrom, K. J. (2006). Ad-
vanced PID control, volume 461. ISA-The Instrumen-
tation, Systems, and Automation Society Research
Triangle Park.
˚
Astr
¨
om, K. J. and Wittenmark, B. (2008). Adaptive control.
Courier Corporation.
Borase, R. P., Maghade, D., Sondkar, S., and Pawar, S.
(2021). A review of pid control, tuning methods and
applications. International Journal of Dynamics and
Control, 9:818–827.
Camacho, O. and Smith, C. A. (2000). Sliding mode con-
trol: an approach to regulate nonlinear chemical pro-
cesses. ISA transactions, 39(2):205–218.
Cha
´
ınho, J., Pereira, P., Rafael, S., and Pires, A. (2005).
A simple pid controller with adaptive parameter in
a dspic; case of study. In Proceedings of the 9th
Spanish-Portuguese Congress on Electrical Engineer-
ing.
Chotikunnan, P. and Chotikunnan, R. (2023). Dual de-
sign pid controller for robotic manipulator applica-
tion. Journal of Robotics and Control (JRC), 4(1):23–
34.
H
¨
agglund, T. and Guzm
´
an, J. L. (2024). Give us pid
controllers and we can control the world. IFAC-
PapersOnLine, 58(7):103–108.
Han, J. (2009). From pid to active disturbance rejection
control. IEEE transactions on Industrial Electronics,
56(3):900–906.
Huang, B. and Shah, S. L. (1999). Performance Assessment
of Control Loops: Theory and Applications. Springer.
Huang, H.-P., Roan, M.-L., and Jeng, J.-C. (2002). On-line
adaptive tuning for pid controllers. IEE Proceedings-
Control Theory and Applications, 149(1):60–67.
Iglesias, E., Garc
´
ıa, Y., Sanjuan, M., Camacho, O., and
Smith, C. (2007). Fuzzy surface-based sliding mode
control. ISA transactions, 46(1):73–83.
Isermann, R. and Isermann, R. (1991). Adaptive control
systems (a short review). Digital Control Systems:
Volume 2: Stochastic Control, Multivariable Control,
Adaptive Control, Applications, pages 127–140.
Liptak, B. G. (2018). Instrument engineers’ handbook, vol-
ume two: Process control and optimization. CRC
press.
Liu, Z.-G., Xue, L., and Zhang, W. (2021). Universal adap-
tive control strategies for stochastic nonlinear time-
delay systems with odd rational powers. Automatica,
125:109419.
ICINCO 2024 - 21st International Conference on Informatics in Control, Automation and Robotics
176