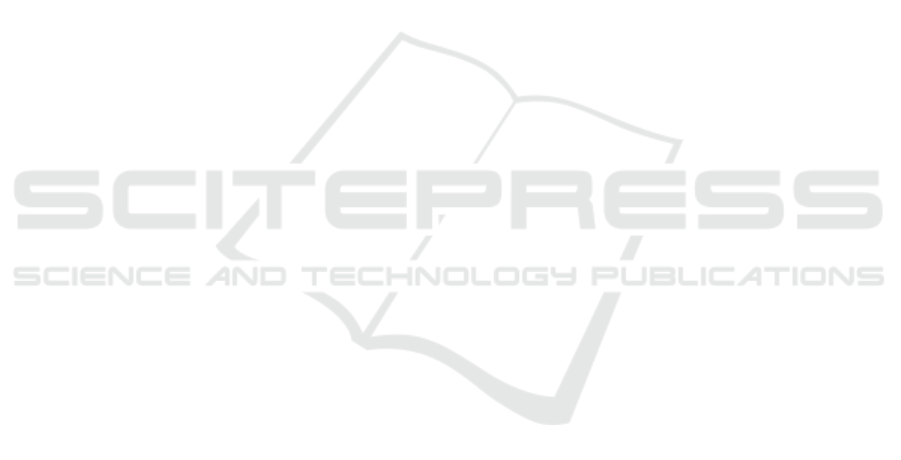
nal with 250 Hz sine flanks is preferred over the pure
rectangular signal.
In another publication, a similar micro pump de-
sign was introduced to enable the delivery of high
viscosity liquids (Surendran et al., 2024). It was
equipped with a piezoelectric stack actuator, thus al-
lowing high pressure actuation while limiting the volt-
age to 200 V. Surendran et al. (2024) also observed
degradation of pump functionality due to actuation
with a rectangular signal, although the overall voltage
amplitude was smaller.
The non-free jetting single-stroke volumes from
Thalhofer et al. (2021) yield 11.1 µl ± 0.1 µl for a
voltage amplitude of [+300 V / -80 V], SRS signal,
and pump stroke frequency below 20 Hz. In the free
jetting setup of our publication, single-stroke volumes
with the same parameters, and fixed frequency of 10
Hz, are at 3.59 µl ± 0.04 µl and 6.57 µl ± 0.32 µl
for the first and second measurement, respectively.
Smaller volumes in the free jetting results, compared
to greater values in Thalhofer et al. (2021), can be
explained by fluid that remained in the tubes or at
the needle’s tip. Moreover, even though the exact
same pump type is used in the compared publica-
tions, each pump within one pump type can be dif-
ferent due to production. However, the results for the
first and second measurement of this paper are dif-
ferent for the same parameters and the same pump
evaluated. Therefore, small differences in the setup
can highly influence the dosed volume. In this pub-
lication, the deviation of the average dosed weight is
used as an indicator for the precision of dosing with
the micro pump. A positive finding is that the devia-
tion for dosed volumes in jetting and non-jetting se-
tups is overall below 5% for the previously described
parameters.
For both publications, it was observed that the
dosed portions for the sinusoidal signal always show
less volume than the SRS packages (Thalhofer et al.,
2021).
5 CONCLUSION
Jet dosing with stainless steel micro diaphragm
pumps is realized and yields reliable minimal jet vol-
umes of 3.59 µl and 3.66 µl for the actuation with a
[+300 V / -80 V] SRS and rectangular signal, respec-
tively. Therefore, they can be implemented in prod-
ucts requiring defined volumes like pipettes.
As the previous comparison of jetting and non-
jetting precision shows very different results due to
comparing different pumps, future research will focus
on the differences of jetting and non-jetting by com-
paring free jet and standard dosing results of the same
pump.
Additionally, it is important to find a method to
characterize and calibrate the presented micro pumps,
as stroke sizes are varying from pump to pump. More-
over, the feasibility of microliter jetting of higher vis-
cose mediums will be investigated to prepare the us-
age of micro pumps in dosing of complex pharmaceu-
ticals.
The results presented in this paper, can enable the
development of a new pipetting technique. The mi-
cro pump provides a jet with a defined volume that
can be delivered contactless into a container, making
the use of disposable pipetting tips obsolete. For this
application, the robustness of free jet microliter dos-
ing using a micro pump must be improved. Replacing
the current single-layered piezoelectric actuator wit a
stack actuator as described by Surendran et al. (2024),
can be beneficial for precision and robustness of free
jetting. Moreover, energy consumption and dosing
volumes can be reduced while achieving liquid jets
with higher velocity, pressure, and viscosity. This can
enable the application of micro pumps in needle-free
subcutaneous injections.
REFERENCES
Bußmann, A. B., Durasiewicz, C. P., Kibler, S. H. A., and
Wald, C. K. (2021). Piezoelectric titanium based mi-
crofluidic pump and valves for implantable medical
applications. Sensors and Actuators A: Physical, page
112649.
Pushparaj, P. N. (2020). Revisiting the micropipetting tech-
niques in biomedical sciences: A fundamental pre-
requisite in good laboratory practice. Bioinformation,
16(1):8–12.
Surendran, N., Durasiewicz, C. P., Hoffmann, T., Wille, A.,
Bussmann, A. B., and Richter, M. (2024). Microflu-
idic delivery of high viscosity liquids using piezo-
electric micropumps for subcutaneous drug infusion
applications. IEEE Open Journal of Engineering in
Medicine and Biology, 5:21–31.
Thalhofer, T., Bussmann, A. B., Durasiewicz, C. P., and
Hayden, O. (2021). Effect of actuation signal on sin-
gle stroke volume in metal micro diaphragm pumps.
International Conference and Exhibition on New Ac-
tuator Systems and Applications.
Wackerle, M., Drost, A., and Richter, M. (2002). A novel
device for high frequency ejection of nanoliter jets:
Actuator, international conference on new actuators,
8, international exhibition on smart actuators and drive
systems, 2, 2002, pp.227-230.
Wald, C., Richter, M., Holzer, M., and Weigl, M. (2013).
Concept of a novel stainless-steel micro pump for ap-
plications in medicine and biotechnology. Mikrosys-
temtechnik Kongress 2013.
BIODEVICES 2025 - 18th International Conference on Biomedical Electronics and Devices
118