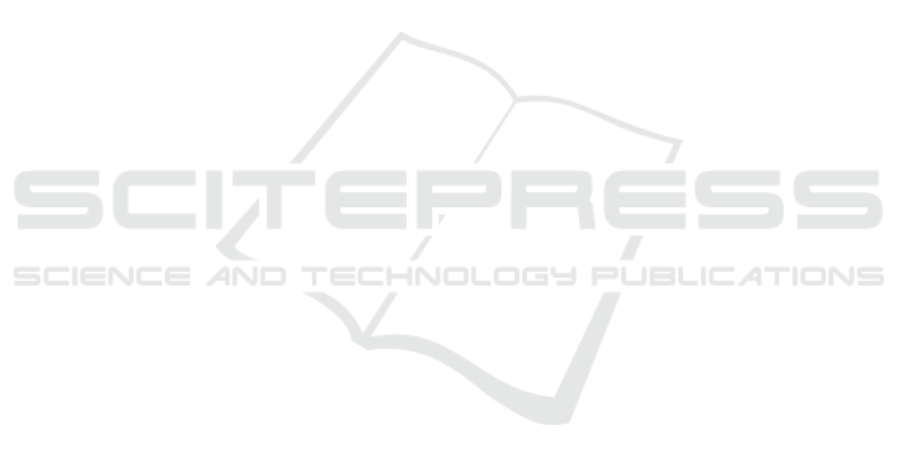
cost: Analysis of different market value and labor cost
for reused parts in german and japanese cases. Inter-
national Journal of Production Economics, 213:229–
242.
Herczeg, G., Akkerman, R., and Hauschild, M. Z. (2018).
Supply chain collaboration in industrial symbiosis
networks. Journal of cleaner production, 171:1058–
1067.
Hoveling, T., Nijdam, A. S., Monincx, M., Faludi, J., and
Bakker, C. (2024). Circular economy for medical de-
vices: Barriers, opportunities and best practices from
a design perspective. Resources, Conservation and
Recycling, 208:107719.
Khodier, A., Williams, K., and Dallison, N. (2018). Chal-
lenges around automotive shredder residue production
and disposal. Waste Management, 73:566–573.
Kinoshita, Y., Yamada, T., Gupta, S. M., Ishigaki, A.,
and Inoue, M. (2016). Disassembly parts selection
and analysis for recycling rate and cost by goal pro-
gramming. Journal of Advanced Mechanical Design,
Systems, and Manufacturing, 10(3):JAMDSM0052–
JAMDSM0052.
Kirchherr, J., Yang, N.-H. N., Schulze-Sp
¨
untrup, F.,
Heerink, M. J., and Hartley, K. (2023). Conceptual-
izing the circular economy (revisited): an analysis of
221 definitions. Resources, Conservation and Recy-
cling, 194:107001.
Kravchenko, M., Pigosso, D. C., and McAloone, T. C.
(2019). Towards the ex-ante sustainability screening
of circular economy initiatives in manufacturing com-
panies: Consolidation of leading sustainability-related
performance indicators. Journal of Cleaner Produc-
tion, 241:118318.
Lahane, S., Kant, R., and Shankar, R. (2020). Circular
supply chain management: A state-of-art review and
future opportunities. Journal of Cleaner Production,
258:120859.
Mangla, S. K., Luthra, S., Mishra, N., Singh, A., Rana,
N. P., Dora, M., and Dwivedi, Y. (2018). Barriers to
effective circular supply chain management in a devel-
oping country context. Production Planning & Con-
trol, 29(6):551–569.
Mishra, J. L., Hopkinson, P. G., and Tidridge, G. (2018).
Value creation from circular economy-led closed loop
supply chains: a case study of fast-moving consumer
goods. Production Planning & Control, 29(6):509–
521.
Nasir, M. H. A., Genovese, A., Acquaye, A. A., Koh, S.,
and Yamoah, F. (2017). Comparing linear and circu-
lar supply chains: A case study from the construction
industry. International Journal of Production Eco-
nomics, 183:443–457.
NHS (2022). Delivering a ‘net zero’ national
health service. https://www.england.nhs.uk/
greenernhs/wp-content/uploads/sites/51/2022/07/
B1728-delivering-a-net-zero-nhs-july-2022.pdf.
Accessed: 2024-09-24.
Nicholson, A. L., Olivetti, E. A., Gregory, J. R., Field, F. R.,
and Kirchain, R. E. (2009). End-of-life lca allocation
methods: Open loop recycling impacts on robustness
of material selection decisions. In 2009 IEEE interna-
tional symposium on sustainable systems and technol-
ogy, pages 1–6. IEEE.
Pichler, P.-P., Jaccard, I. S., Weisz, U., and Weisz, H.
(2019). International comparison of health care
carbon footprints. Environmental research letters,
14(6):064004.
Ranta, V., Aarikka-Stenroos, L., Ritala, P., and M
¨
akinen,
S. J. (2018). Exploring institutional drivers and bar-
riers of the circular economy: A cross-regional com-
parison of china, the us, and europe. Resources, Con-
servation and Recycling, 135:70–82.
Romanello, M., Di Napoli, C., Green, C., Kennard, H.,
Lampard, P., Scamman, D., Walawender, M., Ali, Z.,
Ameli, N., Ayeb-Karlsson, S., et al. (2023). The 2023
report of the lancet countdown on health and climate
change: the imperative for a health-centred response
in a world facing irreversible harms. The Lancet,
402(10419):2346–2394.
Rosa, P., Sassanelli, C., and Terzi, S. (2019). Circular busi-
ness models versus circular benefits: An assessment
in the waste from electrical and electronic equipments
sector. Journal of cleaner production, 231:940–952.
Roy, T., Garza-Reyes, J. A., Kumar, V., Kumar, A., and
Agrawal, R. (2022). Redesigning traditional linear
supply chains into circular supply chains–a study into
its challenges. Sustainable Production and Consump-
tion, 31:113–126.
Tura, N., Hanski, J., Ahola, T., St
˚
ahle, M., Piiparinen, S.,
and Valkokari, P. (2019). Unlocking circular busi-
ness: A framework of barriers and drivers. Journal
of cleaner production, 212:90–98.
Vermunt, D. A., Negro, S. O., Verweij, P. A., Kuppens,
D. V., and Hekkert, M. P. (2019). Exploring barri-
ers to implementing different circular business mod-
els. Journal of cleaner production, 222:891–902.
Watkins, C. J. C. H. (1989). Learning from delayed rewards.
Winkler, H. (2011). Closed-loop production systems—a
sustainable supply chain approach. CIRP Journal
of Manufacturing Science and Technology, 4(3):243–
246.
Enhancing Circularity in Medical Device Supply Chains by Optimizing EoL Decisions Through Reinforcement Learning: A
Multi-Objective Approach
99