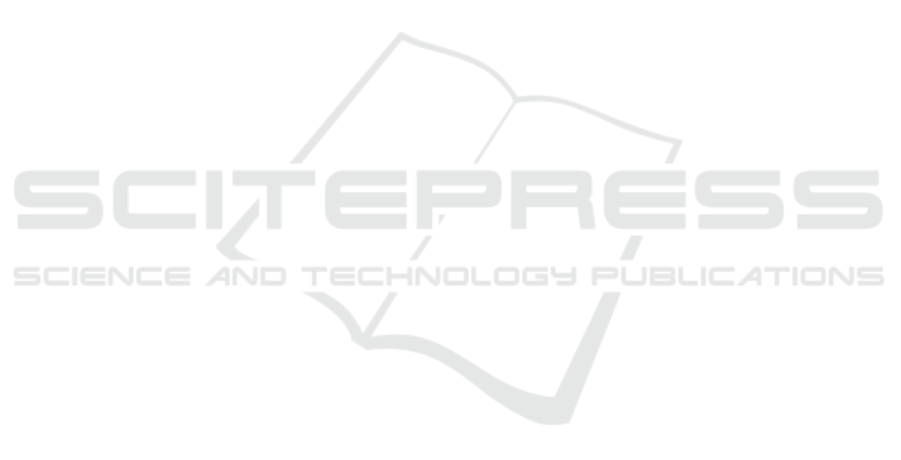
though the hysteresis on the capacitance of the
devices has values slightly bigger (20.7% on average)
than the mechanical hysteresis (16.9 % on average),
the hysteresis of the resistance was generallly lower.
However, it is important to notice that between each
material considered, there were wide differences
ranging between the mechanical hysteresis of TPE
(24.5%) to one of the micro-structured devices
(5.9%). Considering the maximum available load, the
filled materials could withstand higher loads of up to
1200 N in general. On the other hand, the micro-
structured one was less stiff and could withstand up
to 90 N, with a stunning 13x increase in sensitivity
concerning TPU. This outcome suggests the
possibility of tuning the device stiffness and its
equivalent relative dielectric constant. Considering
these factors, it may be possible in future works to
produce specific devices with an increased sensitivity
even at low loads. Finally, the full recovery of the
deformation guaranteed by the microstructured
system makes it a promising candidate for multiple-
cycle applications, where this requirement is
mandatory. Even though some of these results are
already reported in the literature, the use of fully 3D
printed structures is still fairly uncommon (Sharma et
al., 2022; Zong et al., 2025). It is also relevant that the
achieved results in terms of sensitivity and working
range seems comparable to the ones reported in the
literature (Li et al., 2024; Zong et al., 2025), even
though further research is needed in order to fully
exploit the capabilities and flexibility of the proposed
approach.
ACKNOWLEDGEMENTS
This study was carried out within the MICS (Made in
Italy – Circular and Sustainable) Extended
Partnership and received funding from the European
Union Next-GenerationEU (PIANO NAZIONALE
DI RIPRESA E RESILIENZA (PNRR) – MISSIONE
4 COMPONENTE 2, INVESTIMENTO 1.3 – D.D.
1551.11-10-2022, PE00000004). This manuscript
reflects only the authors’ views and opinions, neither
the European Union nor the European Commission
can be considered responsible for them.
REFERENCES
Afridi, A., Al Rashid, A., & Koç, M. (2024). Recent
advances in the development of stereolithography-
based additive manufacturing processes: A review of
applications and challenges. Bioprinting, 43, e00360.
https://doi.org/10.1016/j.bprint.2024.e00360
Bianchini, D., Fapanni, T., Garda, M., Leotta, F., Mecella,
M., Rula, A., & Sardini, E. (2024). Digital Thread for
Smart Products: A Survey on Technologies,
Challenges and Opportunities in Service-Oriented
Supply Chains. IEEE Access.
https://doi.org/10.1109/ACCESS.2024.3454375
Borghetti, M., Cantu, E., Sardini, E., & Serpelloni, M.
(2021). Printed Sensors for Smart Objects in Industry
4.0. 6th International Forum on Research and
Technology for Society and Industry, RTSI 2021 -
Proceedings, 57–62.
https://doi.org/10.1109/RTSI50628.2021.9597209
Chortos, A., Liu, J., & Bao, Z. (2016). Pursuing prosthetic
electronic skin. Nature Materials, 15(9), 937–950.
https://doi.org/10.1038/nmat4671
El Hasnaoui, M., Triki, A., Graça, M. P. F., Achour, M. E.,
Costa, L. C., & Arous, M. (2012). Electrical
conductivity studies on carbon black loaded ethylene
butylacrylate polymer composites. Journal of Non-
Crystalline Solids, 358(20), 2810–2815.
https://doi.org/10.1016/j.jnoncrysol.2012.07.008
Fapanni, T., Rosa, R., Cantù, E., Agazzi, F., Lopomo, N.,
Rosace, G., & Sardini, E. (2024). Overall Additive
Manufacturing of Capacitive Sensors Integrated into
Textiles: A Preliminary Analysis on Contact Pressure
Estimation. Proceedings of the 17th International
Joint Conference on Biomedical Engineering Systems
and Technologies, 195–200.
https://doi.org/10.5220/0012597000003657
Gao, L., Zhu, C., Li, L., Zhang, C., Liu, J., Yu, H.-D., &
Huang, W. (2019). All Paper-Based Flexible and
Wearable Piezoresistive Pressure Sensor. ACS Applied
Materials & Interfaces, 11(28), 25034–25042.
https://doi.org/10.1021/acsami.9b07465
José Horst, D., & De Almeida Vieira, R. (2018). Additive
Manufacturing at Industry 4.0: a Review. In
International Journal of Engineering and Technical
Research (Issue 8). www.erpublication.org
Kortuem, G., Kawsar, F., Fitton, D., & Sundramoorthy, V.
(2010). Internet of Things Track Smart Objects as
Building Blocks for the Internet of Things.
www.computer.org/internet/
Laszczak, P., Jiang, L., Bader, D. L., Moser, D., & Zahedi,
S. (2015). Development and validation of a 3D-printed
interfacial stress sensor for prosthetic applications.
Medical Engineering & Physics, 37(1), 132–137.
https://doi.org/10.1016/j.medengphy.2014.10.002
Li, P., Zhang, Y., Li, C., Chen, X., Gou, X., Zhou, Y.,
Yang, J., & Xie, L. (2024). From materials to
structures: a holistic examination of achieving linearity
in flexible pressure sensors. In Nanotechnology (Vol.
36, Issue 4). https://doi.org/10.1088/1361-
6528/ad8750
Mannsfeld, S. C. B., Tee, B. C.-K., Stoltenberg, R. M.,
Chen, C. V. H.-H., Barman, S., Muir, B. V. O.,
Sokolov, A. N., Reese, C., & Bao, Z. (2010). Highly
sensitive flexible pressure sensors with
microstructured rubber dielectric layers. Nature
BIODEVICES 2025 - 18th International Conference on Biomedical Electronics and Devices
186