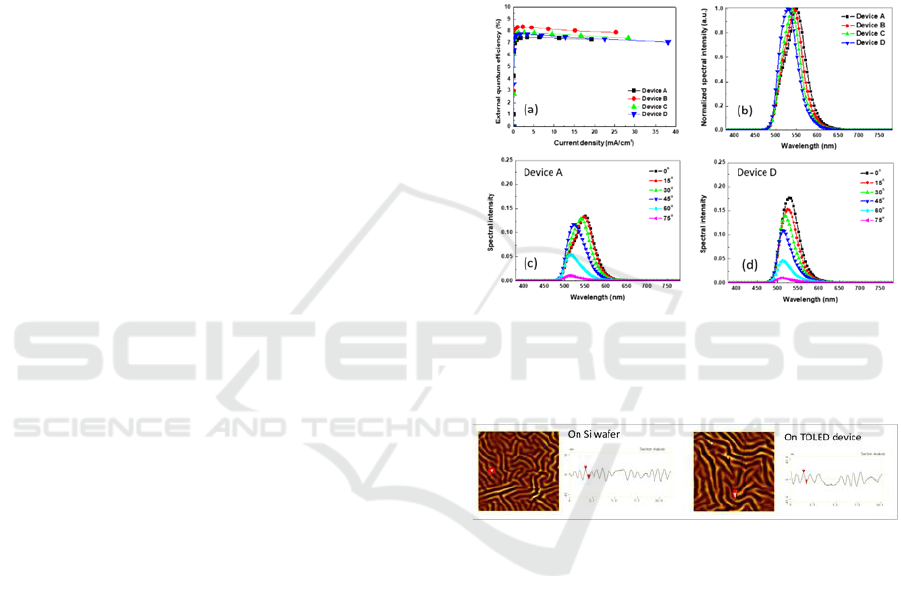
evaporation without breaking vacuum. Aluminum
layer was deposited on glass substrate as a reflective
anode electrode having a thickness of 100 nm.
Afterwards, 2 nm-thick MoO
3
layer for hole injection
and buffer, 28 nm-thick TCTA layer for hole
transport, 30 nm-thick EML layer of doped co-host
system (TCTA : TmPyPB : Ir(ppy)
3
= 0.465 : 0.465 :
0.07), 25 nm-thick TmPyPB layer for electron
transport, 0.5 nm-thick LiF layer and 1 nm-thick Al
layer for electron injection, and 18 nm-thick Ag layer
for composite semi-transparent cathode electrode
were deposited. Surface morphology of sample was
measured by atomic force microscopy (AFM, Veeco
Instruments) and scanning electron microscope
(SEM), etc. Fabricated TOLEDs were characterized
using a source meter (Keithley 2400) with a
spectrometer (PR655, Photo Research) and custom-
built goniometer for angular dependence measure-
ment of light emission. All electroluminescence
spectra and angular emission patterns were recorded
at a constant current density of 10mA/cm
2
with a
spectrometer
2.3 Results of Device Data: Improved
LE and Viewing Angle Behavior
Fig 3 (a) illustrates current density - external quantum
efficiency behavior of TOLED with 1D wavy
underneath of entire layers. The devices with wavy
pattern showed slightly higher current density than
references. At the inflection point of these sinusoidal
patterns, the thickness of the organic layer is partially
thinned, which might result in the formation of a
stronger local electric field. Luminance tended to
increase as the depth of the wavy pattern increases,
however, EQE values are only slightly increased at
device B (low-height 1D wavy) compared to
reference device A, showing only similar values of
7.73 and 7.56% for devices with higher 1D patterns
(device C and D, respectively). Fig 3b shows
normalized spectral intensity in the normal direction
of the emitting surface. The sinusoidal wavy pattern
gradually changes the microcavity length of the
TOLED. The thickness of the cavity length (organic
layer) became thinner at the inflection point and
thickens at the trough peak (Liu et al. 2012). With the
height of wavy patterns inside TOLED increases, the
micro-cavity effect starts to be reduced, so that
angular dependence of the spectrum for device D is
less-sensitive compared with reference device A.
However, overall performance of wave LE layer was
not great for these structures.
Fig 4 illustrate the representative image obtained
by AFM for 2D random wavy patterns that organic
bi-layers with thermal expansivity difference
generates. The pitch and depth of patterns could be
systematically controlled, depending on the annealing
temperature and time. The Si wafer and the buckling
structure formed on the top of the TOLED are shown
in Fig 4a and 4b, respectively. For example, 35nm
N,N’-Bis(3-methylphenyl)-N,N’-diphenylbenzidine
(TPD) and 15nm tris(8-hydroxy-quinolinato)
aluminum (Alq
3
) deposited and annealed at a
temperature of 80°C were shown. The both measured
patterns had 750 nm pitch and 30 nm depth.
Figure 3: (a) Current density v. EQE, (b) spectral response
(c)(d) angular dependence per each viewing angle for
device A and D, without and with 1D micron scale wavy
pattern. Devices are identical with structures in Fig. 2.
Figure 4: AFM image of 2D buckling structure formed by
spontaneous thermal expansion/compression (a) on the Si
wafer substrate and (b) on the TOLED device (scan size: 10
x 10 μm).
Since the formation of buckling 2D wavy patterns
formed on top of the transparent cathode of TOLED
does not affect the thermal state of the underlying
organic layer of devices, micro-cavity of those
TOLEDS were well maintained. Devices in Fig 5a
showed; the layout of LE bucking structures, where
device A (EQE 12.4 represents the reference without
LE, device B shows non-bucking LE with same
organic bi-layer. For devices of C, D, and E, wavy
pattern pitch/depth is 750/30, 1000/45, and 1150/64
(nm), respectively. The improvement of external
quantum efficiencies were significant in case of
TOLEDs with 2D buckling, where the most
optimized devices E showed 21% (reference A and
PHOTOPTICS 2025 - 13th International Conference on Photonics, Optics and Laser Technology
144