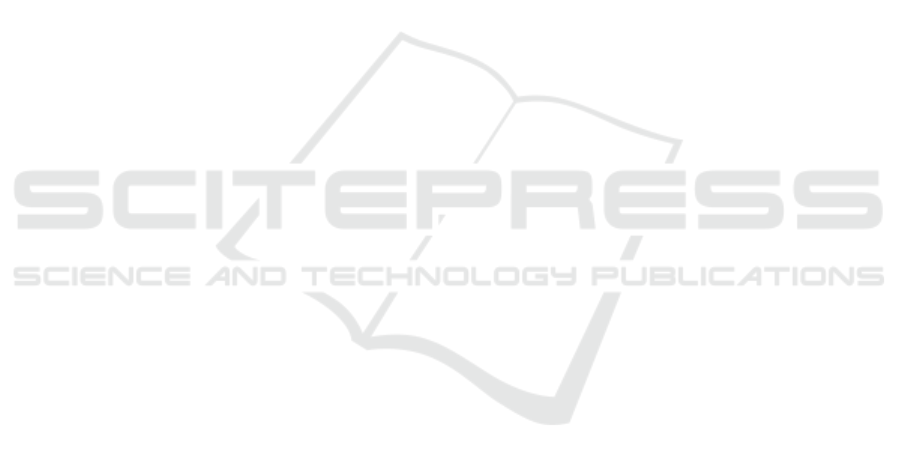
Giunta, L., Hicks, B., Snider, C., and Gopsill, J. (2023).
A living lab platform for testing additive manufactur-
ing agent-based manufacturing strategies. Procedia
CIRP, 119:656–661.
Goldhar, J. D. and Jelinek, M. (1990). Manufacturing as a
service business: Cim in the 21st century. Computers
in Industry, 14(1-3):225–245.
Ivanov, D., Dolgui, A., and Sokolov, B. (2022). Cloud sup-
ply chain: Integrating industry 4.0 and digital plat-
forms in the “supply chain-as-a-service”. Transporta-
tion Research Part E: Logistics and Transportation
Review, 160:102676.
Ivki
´
c, I., Buhmann, T., List, B., and Gnauer, C. (2024).
Towards a cost-benefit analysis of additive manufac-
turing as a service. In Proceedings of the 14th In-
ternational Conference on Cloud Computing and Ser-
vices Science - CLOSER, pages 338–345. INSTICC,
SciTePress.
Jagoda, J., Diggs-McGee, B., Kreiger, M., and Schuldt,
S. (2020). The viability and simplicity of 3d-printed
construction: A military case study. Infrastructures,
5(4):35.
Lee, J. M.-y. and Wong, E. Y.-c. (2021). Suez canal block-
age: an analysis of legal impact, risks and liabilities
to the global supply chain. In MATEC web of confer-
ences, volume 339, page 01019. EDP Sciences.
Lu, Y. and Xu, X. (2019). Cloud-based manufacturing
equipment and big data analytics to enable on-demand
manufacturing services. Robotics and Computer-
Integrated Manufacturing, 57:92–102.
Lu, Y., Xu, X., and Xu, J. (2014). Development of a hy-
brid manufacturing cloud. Journal of manufacturing
systems, 33(4):551–566.
Mai, J., Zhang, L., Tao, F., and Ren, L. (2016). Customized
production based on distributed 3d printing services
in cloud manufacturing. The International Journal of
Advanced Manufacturing Technology, 84:71–83.
Mugurusi, G. and de Boer, L. (2013). What follows after the
decision to offshore production? a systematic review
of the literature. Strategic Outsourcing: An Interna-
tional Journal, 6(3):213–257.
Nie, J., Xu, X., Yue, X., Guo, Q., and Zhou, Y. (2023).
Less is more: A strategic analysis of 3d printing with
limited capacity. International Journal of Production
Economics, 258:108816.
Pahwa, D. and Starly, B. (2021). Dynamic match-
ing with deep reinforcement learning for a two-
sided manufacturing-as-a-service (maas) marketplace.
Manufacturing Letters, 29:11–14.
Panda, S. K., Rath, K. C., Mishra, S., and Khang, A. (2023).
Revolutionizing product development: The growing
importance of 3d printing technology. Materials To-
day: Proceedings.
Rankin, T. M., Giovinco, N. A., Cucher, D. J., Watts, G.,
Hurwitz, B., and Armstrong, D. G. (2014). Three-
dimensional printing surgical instruments: are we
there yet? Journal of Surgical Research, 189(2).
Rauch, E., Unterhofer, M., and Dallasega, P. (2018). In-
dustry sector analysis for the application of additive
manufacturing in smart and distributed manufacturing
systems. Manufacturing Letters, 15:126–131.
Rudolph, J.-P. and Emmelmann, C. (2017). A cloud-based
platform for automated order processing in additive
manufacturing. Procedia Cirp, 63:412–417.
Schwilling, T., Schulze, I., Wilts, H., and Du Bois, P.
(2021). Circular economy 2021. secondhand in
deutschland.
Shahrubudin, N., Lee, T. C., and Ramlan, R. (2019). An
overview on 3d printing technology: Technological,
materials, and applications. Procedia manufacturing,
35:1286–1296.
Simeone, A., Caggiano, A., and Zeng, Y. (2020). Smart
cloud manufacturing platform for resource efficiency
improvement of additive manufacturing services. Pro-
cedia Cirp, 88:387–392.
ˇ
Skulj, G., Vrabi
ˇ
c, R., Butala, P., and Sluga, A. (2017). De-
centralised network architecture for cloud manufac-
turing. International Journal of Computer Integrated
Manufacturing, 30(4-5):395–408.
Smith, S., Smith, G. C., Jiao, R., and Chu, C.-H. (2013).
Mass customization in the product life cycle. Journal
of Intelligent Manufacturing, 24:877–885.
Sun, M., Ng, C. T., Yang, L., and Zhang, T. (2024).
Optimal after-sales service offering strategy: Addi-
tive manufacturing, traditional manufacturing, or hy-
brid? International Journal of Production Economics,
268:109116.
Tao, F., Cheng, Y., Zhang, L., and Nee, A. Y. (2017). Ad-
vanced manufacturing systems: socialization charac-
teristics and trends. Journal of Intelligent Manufac-
turing, 28:1079–1094.
Thames, L. and Schaefer, D. (2017). Industry 4.0: An
overview of key benefits, technologies, and chal-
lenges. Cybersecurity for Industry 4.0: Analysis for
Design and Manufacturing, pages 1–33.
Url, P., Stampfl, D., T
¨
odtling, M., and Vorraber, W.
(2022). Challenges of an additive manufacturing
service platform for medical applications. Procedia
CIRP, 112:400–405.
Vedeshin, A., Dogru, J. M. U., Liiv, I., Draheim, D.,
and Ben Yahia, S. (2019). A digital ecosystem for
personal manufacturing: an architecture for cloud-
based distributed manufacturing operating systems. In
Proceedings of the 11th International Conference on
Management of Digital EcoSystems, pages 224–228.
Wang, Y., Zheng, P., Xu, X., Yang, H., and Zou, J.
(2019). Production planning for cloud-based ad-
ditive manufacturing—a computer vision-based ap-
proach. Robotics and Computer-Integrated Manufac-
turing, 58:145–157.
Westk
¨
amper, E. and L
¨
offler, C. (2016). Strategien der
produktion-technologien. Konzepte und Wege in die
Praxis, 1(2.1).
Wong, K. V. and Hernandez, A. (2012). A review of addi-
tive manufacturing. International scholarly research
notices, 2012(1):208760.
Wu, D., Greer, M. J., Rosen, D. W., and Schaefer, D.
(2013). Cloud manufacturing: Strategic vision and
state-of-the-art. Journal of Manufacturing Systems,
32(4):564–579.
Xu, X. (2012). From cloud computing to cloud manufac-
turing. Robotics and computer-integrated manufac-
turing, 28(1):75–86.
Zhang, L., Luo, Y., Tao, F., Li, B. H., Ren, L., Zhang, X.,
Guo, H., Cheng, Y., Hu, A., and Liu, Y. (2014). Cloud
manufacturing: a new manufacturing paradigm. En-
terprise Information Systems, 8(2):167–187.
CLOSER 2025 - 15th International Conference on Cloud Computing and Services Science
230